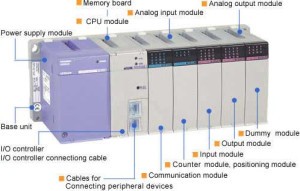
Programmable Logic Controller
Programmable Logic Controller (PLC) is a special computer device used in industrial control systems. Due to its robust construction, exceptional functional features like sequential control, counters and timers, ease of programming, reliable controlling capabilities and ease of hardware usage – this PLC is used as more than a special-purpose digital computer in industries as well as in other control-system areas. Most of the industries abbreviate these devices as “PC” but it is also used for personal computers; due to this, many manufacturers named these devices as PLCs.
The programmable logic controller is used not only for industrial purpose but also in civil applications such as washing machine, elevators working and traffic signals control. Different types of PLCs from a vast number of manufacturers are available in today’s market. Therefore, in the following paragraphs, let us study about programmable logic controller’s basics, principles and applications.
Principle of Programmable Logic Controller:
Programmable Logic Controllers are used for continuously monitoring the input values from sensors and produces the outputs for the operation of actuators based on the program. Every PLC system comprises these three modules:
- CPU module
- Power supply module
- One or more I/O module
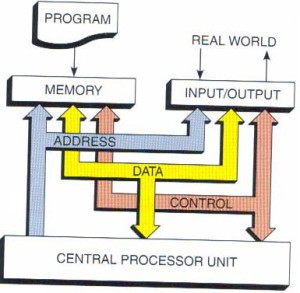
PLC Architecture
CPU Module:
A CPU module consists of central processor and its memory. The processor is responsible for performing all the necessary computations and processing of data by accepting the inputs and producing the appropriate outputs.
Power Supply Module:
This module supplies the required power to the whole system by converting the available AC power to DC power required for the CPU and I/O modules. The 5V DC output drives the computer circuitry.
I/O Modules:
The input and out modules of the programmable logic controller are used to connect the sensors and actuators to the system to sense the various parameters such as temperature, pressure and flow, etc. These I/O modules are of two types: digital or analog.
Communication Interface Modules:
These are intelligent I/O modules which transfers the information between a CPU and communication network. These communication modules are used for communicating with other PLC’s and computers, which are placed at remote place or far-off locate.
The program in the CPU of programmable logic controller consists of operating system and user programs. The purpose of the operating system with CPU is to deal with the tasks and operations of the PLC such as starting and stopping operations, storage area and communication management, etc. A user program is used by the user for finishing and controlling the tasks in automation.
The Principle of operation of the PLC can be understood with the cyclic scanning also called as scan cycle, which is given in the below figure.
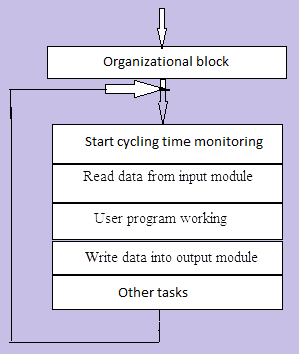
PLC Scan Cycle
A typical PLC scans cycle includes of the following steps:
- The operating system starts cycling and monitoring of time.
- The CPU starts reading the data from the input module and checks the status of all the inputs.
- The CPU starts executing the user or application program written in relay-ladder logic or any other PLC-programming language.
- Next, the CPU performs all the internal diagnosis and communication tasks.
- According to the program results, it writes the data into the output module so that all outputs are updated.
- This process continues as long as the PLC is in run mode.
To get an idea about the PLC operation,consider the simple mixer process control as shown in the figure below.
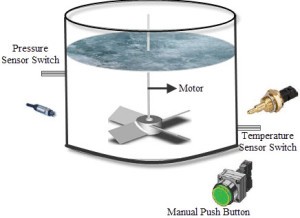
Simple Mixer Process Control
In the above figure, the set up has a mixer motor to stir liquid automatically in the container whenever the temperature and pressure reaches the preset values. In addition, a separate manual push button station is used for the operation of the motor.The process is monitored with a pressure-sensor switch and temperature-sensor switch. These switches close their respective contacts when conditions reach their preset values.
The input field devices like pressure switch, temperature switch and manual push buttons are hardwired to an appropriate input module, and the output device like motor-starter coil is hardwired to an appropriate output module of the PLC. Based on the program done in the PLC, the system continuously scans all the input preset values and correspondingly updates the outputs, i.e., when both the pressure and temperature switches get energized or the push button gets energized, the PLC automatically energizes the motor-starter coil so that a stirring action takes place.
Applications of Programmable Logic Controller (PLC)
The PLC can be used in industrial departments of all the developed countries in industries like chemical industry, automobile industry, steel industry and electricity industry. Based on the development of all these technologies, functionality and application, the scope of the PLC increases dramatically.
1. Application of PLC in Glass Industry
From the year 1980 the Programmable-logic controllers are in use in the glass industry, and they are assembled bit by bit. PLCs are used mainly in every procedure and workshop for controlling the material ratio, processing of flat glasses, etc.
With the development of PLC and increasing demand in the real world, the control mode of the programmable-logic controller with an intelligent device is applied in the glass industry. In making of a float glass, PLC itself cannot finish some controlling tasks because of the complexity of the control system and processing of huge data. For the production of glass, we make use of bus technology to construct the control mode of a PLC with a distributed-control system. This control system deals with analog controlling and data recording; the PLC is also used for digital quality control and position control.
This type of control mode is a big advantage for PLC and DCS for improving reliability and flexibility of the control system.
2. Applications of PLC in Cement Industry
Along with the best-quality raw materials, the accurate data regarding process variables, especially during mixing processes within the kiln, ensures that the output provided should be of the best possible quality. Nowadays a DCS with bus technology is used in the production and management industry. By using this existing DCS control system, the PLC is in user mode of SCADA. This mode comprises PLC and configuration software. This SCADA mode comprises the PLC and host computer. The host computer consists of slave and master station. The PLC is used for controlling the ball milling, shaft kiln and Kiln of coal.
To know more about these programmable-logic controllers’ function, you can go through the following project, which is given as a practical example used mostly for industrial automation.
Thus, this article has covered the principle of operation of programmable logic devices or controller and its applications in various industries like glass industry, steel industry and cement industry. For any help regarding this topic, please contact us by commenting in the comment section given below.
Photo Credits:
- Programmable Logic Controller by rocatek