A device that gives the motor some initiation to start safely is known as Starter. Similarly, the three-point starter is common for the starting purpose which is used to start DC compound or shunt motors. While starting DC shunt motor it draws huge current from the line which damages the internal parts of the motor. So, a three-point starter helps in limiting the starting current such that the motor begins to attain speed slowly and runs smoothly. Depending upon the rating and size of the motor suitable starter will be selected.
What is a Three-point Starter?
It is named as a 3-point starter because this starter has 3 terminals, one is L (line) linked to supply, one is F (field) linked to the field and the other is A (armature) linked to the armature. The starter box contains some parts such as the spring, handle and an electromagnetic coil. The handle moves the soft iron piece affixed to it which is of some insulating material. The soft iron material is attracted by the electromagnetic coil when it is energized. The spring produces some opposing force to that of an electromagnetic coil.
What is the Need for Using a Three-Point Starter?
The three-point starter reduces the high initial currents that arise while starting the motor in order to protect the equipment.
Working Principle of a Three-Point Starter?
The three-point starter commissions on the principle of electromagnetic attraction. When current passes through the electromagnetic coil it gets energized. Further, the flux produced around attracts the soft iron piece linked to the handle.
Construction of a Three-Point Starter
- Line L1 is connected directly to an electromagnet through which current passes. The soft iron piece is attached to the electromagnet has a notch which is of conducting material. The handle is attached to a spring which opposes the force of electromagnet. One terminal of an electromagnet and another terminal from the handle are made available to contact with a notch. But these two are not in contact they are separated by some distance.
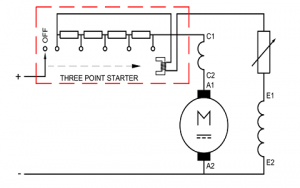
Three-Point Starter
- Another electromagnet is connected to the field winding. The handle is moved on to the studs through resistance connected to the armature. When the handle is moved current flows such that electromagnet gets energized, which attracts the soft iron piece attached to handle. The handle is moved further cutting the resistance (slowly) to its final position such that the motor picks up speed slowly.
Operation of Three-Point Starter
- When we move the handle it gets in contact with the resistance such that the current starts flowing through the coil. Due to the current, the coil gets energized and produces some flux which allows current to flow through the field winding.
- At this point, the field winding is carrying current but no current is flowing through the armature. If we move the handle further contacting studs through the resistance the motor picks up speed slowly. As speed is increasing we will keep moving the handle till its final position cutting some portion of resistance from the circuit. Thus, we can avoid high initial currents.
- At the final position of the starter (handle), the soft iron piece will be attracted by the magnetic flux of the electromagnetic coil.
- Attraction force by this electromagnetic relay on to the handle will be in the clockwise direction and spring force on the handle will be in an Anti-clockwise direction.
- If attraction force is more compared to spring force then handle will be at the final position. By chance, if this spring force is more compared to the electromagnetic force handle will come back to its original position.
- Under normal operating conditions the electromagnetic force is more than spring force such that the handle will be at its final position.
What Happens if There is a Power Failure While Operating Three- Point Starter?
- In the case of a power failure, no current flows and no flux is produced. As there is no flux electromagnetic force will be zero, an only spring force is present. So, the handle will come back to its previous position. The coil helps in opening the starter in case of a power failure, so this coil is called No Volt Coil or No Volt Relay.
What if an Overload Occurs in a Three-Point Starter?
- If overload occurs the armature draws more current than the usual current due to overloading condition. In that case, the current drawn by the armature is more and the line current will increase. Due to the increase in Line current, magnetic flux will increase.
- As magnetic flux is more the attraction force on a soft iron piece is able to move the notch up shorting the two contacts. The current gets bypassed such that no current and flux is produced. Under overloading conditions handle is moved back to its previous position by means of a relay which is called an overload relay.
- Three-point starter functions very well, if there is no voltage(power failure occurs) then starter turns OFF. If an overload current is drawn by the machine then the starter comes back to its original position.
Drawbacks of Three-Point Starter
- Under speed control by using field weakening method, this starter (3-point starter) is failed by turning OFF.
- Since no extra resistance is present in series with the field winding speed regulation is not possible.
- During a fault, condition circuit may get damaged as there is no extra protective resistance present.
- In a three-point starter, NVC is linked directly with the shunt field and high resistance, so there is a chance that NVC is unable to operate if there is a decrease in current excessively.
Applications of Three-Point Starter
- It helps in running Dc shunt motor, limiting the starting current.
- It helps in the case of a power failure I.e during overload and under load conditions
Know more about Direct Online Starter.
To avoid these drawbacks in a three-point starter we developed a four-point starter. Thus, in this article, we had an overview of three-point starter construction, working principle, drawbacks, and applications. Here is a question for the readers, what is the requirement of using a starter?