Pumps have a long period of history and they were into existence from 2000 B.C. To fetch water, the initial tool that was invented was called shadoof. Even it does not function in the mechanical approach, it was widely accepted by many and best serves the pumping activity. The construction of all these stood as the basis for the development of diaphragm pumps and they were into the market from 1854 onwards. The basic invention of the diaphragm pump was done by J. Pease. And now in the 21st century, diaphragm pumps are completely implemented in the pumping activities and there comes more competition in the progression of these devices. Let’s move to know more about this concept.
What is Diaphragm Pump?
The diaphragm pump definition comes under the classification of positive displacement pumps that utilize the grouping of the reciprocating operation of thermoplastic, rubber and Teflon diaphragm. The flowrates of these devices will not fluctuate much with that of discharge pressure which means the pump functions against the specified pump speed. Diaphragm pumps hold the ability to transfer either low, high or medium viscous liquids and even liquids that have extremely huge solid substances. They even manage strong chemicals like acids because they are developed with multiple kinds of diaphragms and body materials.
Working Principle of Diaphragm Pump
In general, the working of a diaphragm pump uses two adaptable diaphragms that have back and forth movements that create a temporary cavity and this section pumps in and expels the liquid through the pump. The two diaphragms function as a partition barrier between the liquid and the air.
In the initial stroke, the two diaphragms are linked through a shaft via the center chamber, here air valve is also positioned. The main functionality of this air valve is to let the compressed air towards the first diaphragm one thus allows to be close to the center chamber. The first diaphragm develops a press stroke that pulls the fluid out from the pump. Whereas the next diaphragm during this time performs a suction stroke. The air which is in the rear section of the second diaphragm makes environmental pressure to push close the liquid towards suction.
And coming to the second diaphragm, when the forced first diaphragm comes to the stroke end, the air movement will get shifted to the backside of the second diaphragm through the air valve. The forced air drives the second diaphragm to be away from the center section which means the first diaphragm is close to the center section. In the second pump cavity, the discharge ball valve is moved away from its seat, whereas in the first pump cavity the reverse function happens. Upon the stroke completion, the air valve directs the air once again to the rear side of the first diaphragm and the cycle will be restarted.
Air Operated Diaphragm Pump
The most popular kind of diaphragm pump is air operated diaphragm pump and these devices utilize compressed air as the power resource. In this type also, a diaphragm has two sections along with inlet and outlet check valves in every section. Through the air spool valve, sir circulates from one section to other and the spool valve is constructed into the pump. The circulation of air pulls out the liquid from one section and drives into the discharge piping whereas the other section is with liquid. In these devices, there will a little pulsation of the discharge movement. And this pulsation can be lessened through the utilization of dampeners in a piping way. These air operated diaphragm pumps will be available in the sizes of ¼” to 4” having low to high flow rates.
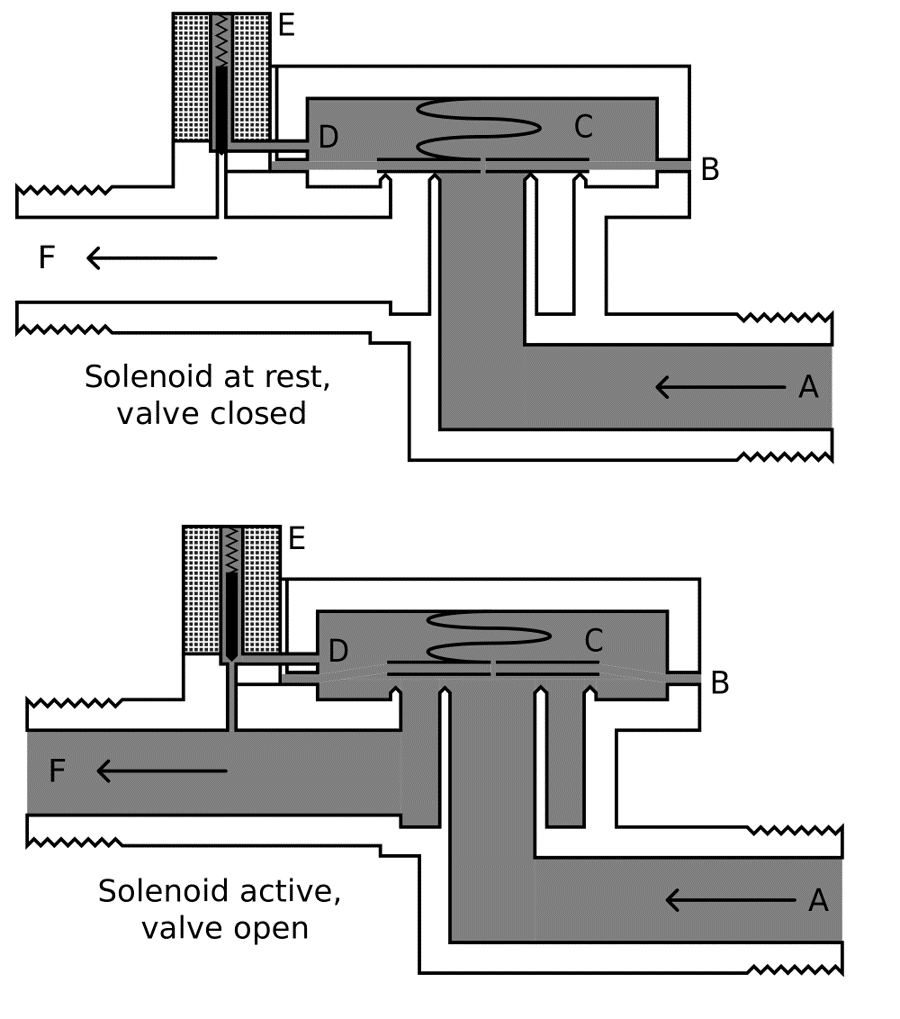
air-operated-diaphragm-pump
The variation in the electric diaphragm water pump and air operated diaphragm pump lies in the pump center chamber where the electric one makes use of electric drive in the place of forced air. In the electric pump, the center chamber is loaded up with forced air and the developed mechanical motion drives the diaphragm to have left and right movement. This front and rear movement will push the liquid to move from one section and towards the outlet, whereas the other section will be filled up by fluid through the inlet, and this process is considered as changeover. The occurred changeover tries to decrease the outlet pulsation.
Diaphragm Pump Diagram
The working principle of the diaphragm pump is almost similar to that of an injection. A syringe is almost the same as like diaphragm pump. When the piston in the pump is pulled back, the liquid will be pulled into the pump and the same when the piston is pushed forward, the liquid will be pulled out. The below picture depicts how a diaphragm pump diagram will be
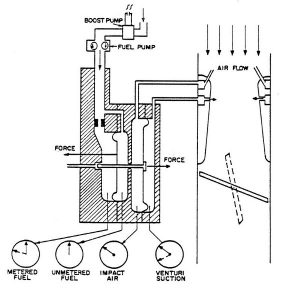
pumping
Advantages & Disadvantages
Diaphragm pumps are extremely implemented for fluid handling requirements. The diaphragm pump advantages & disadvantages are as below:
Advantages
The advantages are
- Manages even strong liquids which have high-level solid content
- They hold the ability to prime themselves
- The pump can be functioned even in dry conditions showing no damage
- As these devices function on air they are innately explosion-proof
- More flexible having only one pump but syncs up well with multiple applications
- Have the capacity to cool themselves
- They are submersible and portable too
- These devices have easy maintenance and inexpensive also
Disadvantages
the disadvantages are
- They have little pulsation which may lead to the device damage
- These pumps are persuaded not to push very accurately at their base section
- Many of the diaphragm pumps typically need 20 cubic feet for every minute & nearly 100 PSI of air consumption to function efficiently.
Diaphragm Pump Applications
Diaphragm pump has many implementations in many domains as every industry mostly require the activity of fluid transmission.
- Used to dewater or water removal in multiple industries
- They can produce enough pressure for spraying and washing applications and are probably utilized for filter press functions.
- Used in abrasive slurry, gels, pharma and oil industries
- Used as shear sensitive foodstuffs
FAQs
1). Can you run a diaphragm pump dry?
For some period of time, running dry diaphragm pumps will not show any kind of harmful effects, while operating for a long period will damage the parts of the device.
2). Are diaphragm pumps reversible?
Yes, diaphragm pumps hold the ability to function against the pressure gradient and so they are reversible.
3). Can diaphragm pumps pump air?
Yes, air operated diaphragm pumps can pump air making compressed air as their power supply.
4). What happens if a pump is not primed?
Before the operation of the pump, they have to be primed or they might not function efficiently.
5). What is the max head of a pump?
The point where the pressure is zero is considered to be the maximum head of the pump.
As there are multiple kinds of diaphragm pumps, based on one’s requirements and characteristic necessity, they need to choose and implement the device. Do all need to know about what are the utmost popular characteristics of a diaphragm pump?