When electrical devices like motor or generator are used in any application, we think that the rotation speed of these devices can be controlled only through the supplied voltage as well as the frequency of the current source. However, an electrical machine’s rotation speed can be exactly controlled by the ‘drive’ concept. By using this concept, motion control can be simply optimized. Now coming to its history, the first electric drive was invented by scientist B.S. lakobi in 1838. In the year 1870, almost universally the electric drive application is seen.
What is Electric Drive?
An electrical drive can be defined as, a system that can be used to handle the movement of electrical machines like motors or generators. This system is designed with an electric motor as well as a control system to manage the rotation of the shaft in the motor.
The prime movers used by this drive mainly include a petrol engine/diesel, steam turbines/gas, electrical & hydraulic motors as the main energy source. These prime movers provide mechanical energy for the drive to control its movement. At present, the movement of the motor can be controlled using the software. So that movement controlling will become more precise.
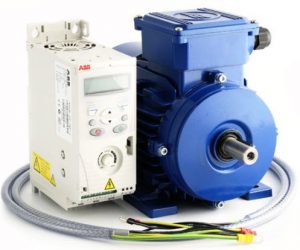
electric-drive
The applications of electric drives mainly include industrial as well as domestic applications such as transportation systems, factories, fans, textile mills, pumps, robots, motors, etc. These drives are used as main movers used for hydraulic & electric motors, petrol or diesel engines, steam or gas turbines.
Types of Electric Drive
Generally, electric drives are available in 3 types namely group, individual, & multi-motor. In addition to these types, these drives are classified into different types depending on the various parameters which include the following.
- Based on the power supply, these drives are classified into two types such as AC drives as well as DC drives.
- Based on the speed, these drives are classified into two types like stable speed drives as well as variable speed drives.
- Based on the motors used, these drives are classified into two type’s namely single motor as well as multi-motor.
- Based on the control parameter, these drives are classified into two types like stable torque and stable power.
Block Diagram of Electric Drive
The electric drive block diagram is shown below and the main parts of this drive include power modulator, motor, control unit as well as a sensing unit. These are explained in detail below.
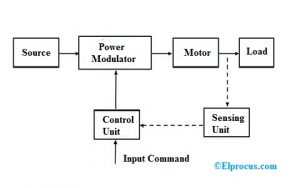
block-diagram-of-electric-drive
Power Modulator
The power modulator mainly controls the o/p power of the supply. The controlling of this can be done from the power source to the electric motor. The motor supplies the speed-torque feature which is necessary through the load.
Throughout the transient functions namely starting, braking & speed reversing, the extreme current will be drawn from the power source. This may cause a voltage drop. So this modulator prevents the source as well as the motor current.
This modulator alters the energy based on the necessity of the motor. For instance, if the power source is direct current and the motor used is induction motor then the power modulator changes direct current to alternate current. It also chooses the operation mode of the electric motor like braking otherwise motoring.
Please refer to this link to know more about Electric Drive
Control Unit
This unit mainly controls the modulator which works with less voltage as well as power levels when required. The power modulator & motor can be protected by the commands generated through the control unit. The input command signal alters the working point of the electric drive from i/p to the control unit.
Sensing Unit
This unit detects the specific parameter of electric drives like motor speed and current. It is mainly used for the operation of closed-loop otherwise protection.
Motor
The electric motor is used for a particular application that can be selected through believing different features like cost, the power reaching level & required act through the load during the active operations and stable state.
Advantages of Electrical Drives
The benefits of electrical drives mainly include the following.
- These drives are available with a wide range of power, torque, and speed.
- They do not pollute the environment.
- It doesn’t require the motor heat up as well as refuel like other types of main movers.
- Presently, the alternating current motor is utilized within changeable speed drives due to the development of semiconductor converters.
- They have flexible characteristics because of electric braking usage.
- Previously, the different motors were used in constant speed drives where variable speed drives employ a dc motor.
Disadvantages of Electrical Drive
The drawbacks of this drive include the following.
- This system is costly.
- It cannot be utilized wherever the current supply is not available.
- The active response is poor.
- The whole system can be stopped by the power breakdown.
- The output power of this drive is low.
- The noise contamination can take place.
Applications of Electrical Drives
The applications of electrical drives include the following.
- These are used in domestic & industrial applications like electric motors, factories, textile mills, fans, transportation systems, pumps, robots, etc.
- These drives are used for electric traction to transport materials from one place to another. Electric tractions are buses, electric trains, trolleys, and vehicles that are power-driven with solar.
- These drives are used for electric traction to transport materials from one place to another. Electric tractions are buses, electric trains, trolleys, and vehicles that are power-driven with solar.
- These are used in spinning machines, conveyor systems, agitators, extruders; draw lines, blowers in yarn, Crain and winding unwinding
- These drives can be used like main movers for engines like petrol/diesel, turbines like gas/steam, motors like hydraulic /electric.
Know more about Conveyor System.
Thus, this is all about detailed information on an electric drive like block diagram, working, types, advantages, disadvantages, and applications. A system used for controlling the motion is named as drives. Sometimes motors are also called drives. Depending on its application, both the drives like AC & DC are used in industries. These drives are economical, pollution-free, give a long life, and easily movable from one location to another. These cannot work in the electricity failure. Here is a question for you, what are the types of the electric drive?