Though there were brushed motors before the design of brushless motors. The first brushed DC motor was invented by a German scientist Ernst Werner Von Siemens in 1856. The challenges involved in the usage of brushed motors are high as it is limited effective and requires higher sustenance. Keeping these challenges in understanding a brushless type has been invented by T.G. Wilson and P.H. Trickey in 1962. The contrivance of this brushless motor led to the development of efficiency and time play in industries. In this article, we shall address a BLDC motor, construction, working, the difference between a normal variety and BLDC, speed control, benefits, limitations, and purposes.
BLDC Motor
Definition: BLDC Motor also known as Brushless DC Motor is a motor-operated without brushes to overcome certain difficulties. The basic difference between a brushed one and BLDC is operating with and without brushes.
A normal machine operates with brushes used to either collect or send current to the commutator. But due to the usage of brushes, sparking occurs at the brush location. As and when the rotor rotates it moves between brushes. At this time, the brushes undergo sparking during the rotation of the shaft. Due to this efficiency decrease and life expectancy are also reduced. To overcome these disadvantages, a BLDC is invented that performs a very smooth operation apart from the normal one. And due to the non-usage of the brushes sparking is also avoided. This increases the life expectancy and efficiency of the motor.
Construction
It consists of a frame in which the rotor and stator are fixed. The rotor is the rotating part and the stator is the stationary part. The frame is used to hold the inner peripherals and also used to protect them from the environment. The rotor is fixed with some permanent magnets and stator has some coils that act as an electromagnet. The number of poles depends upon the operational requirement. The stator has some slots in which the coils are placed. The number of coils to be placed depends upon the number of poles. Depending upon the requirement these coils are energized. The stator winding of this type of motor is shown in the figure below.
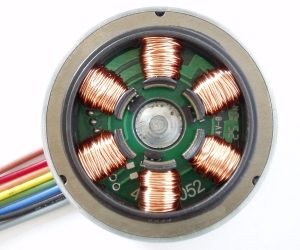
Stator Winding of a Brushless DC Electric Motor
The difference between a permanent magnet and an electromagnet is the permanent magnet has its property inbuilt. But the electromagnet requires some current to pass through the coil to get energized.
Working of BLDC Motor
The BLDC operates on the same law as of a regular type. This type requires some coils to be energized in order to make the rotor rotate. The coils placed in the stator slots are named as A, B, and C. When the coil A is energized by a DC supply, it gets excited and attracts the rotor permanent magnet. Similarly, when the coil B is energized rotor permanent magnet is attracted this continues when the coil C is also energized. After the coil C is energized, the coil A is again energized but with negative polarity. This continues with the remaining coils as well with negative polarity. This cycle continues alternately and the rotor continuously rotates.
But there is a problem of developing the low power output. This can be overcome by connecting the free ends of two coils together I,e A and B. This produces greater power output as the coils energize double the field and pull the rotor permanent magnets along with them. This way a greater output can be achieved.
The problem with the BLDC type is that which coil to energize first. It can be known by finding the position of the rotor coils. This position can be known by using a controller. The controller helps in energizing the coil after receiving the position from the sensor.
A Hall Effect sensor is used for the detection of the position of the coils. The sensor gives this information to the controller. The controller which in turn gives a command for which coil to be energized. The hall effect sensor is shown in the figure below.
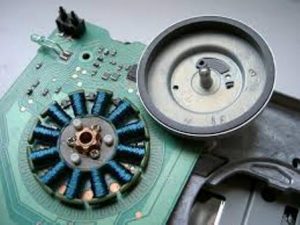
hall sensor Controller
Types
There are two types of BLDC. They are IN-type and Out-type.
It depends upon the construction I,e if the rotor is made to rotate outside then it is Out-type. If the rotor is made to rotate inside then it is considered as IN-type. The most common type used is of Out-type.
Controlling Speed of BLDC Motor
The controlling of the speed of this type is quite as this type includes a controller. The speed control can be possible by adjusting the voltage. Depending upon the amount of voltage supplied to energize the coils the speed can be varied. The voltage supplied to the coils is reduced in order to decrease the speed of the motor.
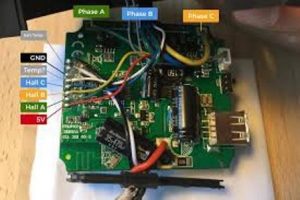
Sensor Control Motor
Advantages
- Highly reliable
- Smoother operation
- High power output
- Can be used for higher speed applications
- No brush is required
- No sparking
- Light in weight
- Less noise
Disadvantages
- Complex operation
- Requires maintenance
- A controller is required
- Costly
- Sensors are required
Applications
It finds its application in small toys, drills machines, AC, PC, servers, trimmers, ventilation fan, air cleaners, projectors, power supply, CCTV, DVR, mixer grinders, hairdryers, and electronic cars or bikes.
Hence, we have discussed what is a BLDC motor. It is a motor that operates without brushed in order to produce a smoother and efficient operation. We have also discussed its construction, working, the difference between a normal and brushed type, speed control, uses, defects, and application. Here is a question for the readers, what is a commutation in DC machines and why a commutator is used?