Before knowing the detailed description and working of the conveyor system let us see know its history and how the device development happened. The initial and fundamental conveyor belt invention took place in the 19th century. While in the period 1892, Thomas Robins invented a conveyor belt that was mainly employed for carrying ore, coal-related materials. In the period 1908, Hymel Goddard first acquired rights on roller conveyors, and in 1913, Henry Ford initiated using these belts for industrial applications. While in the 1920s, conveyors were started to replace rail lines and locomotives in mining and processing activities. And this article now explains conveyor system design, working principle, cleaning system, types, and applications.
What is Conveyor System?
A conveyor system is considered as the fundamental piece of mechanical controlling device which is used for transportation of products, goods, and another kind of equipment across various locations. The locations can be in the same area, building or between different places. These are particularly helpful for businesses that manage huge goods, sharp things, raw products, huge machinery, and other products.
The conveyor belt system is even employed for speed and effective shipping of business equipment along with huge devices like cars down like manufacturing line where these make them in prevalent in material management and packing industries along with the production industries.
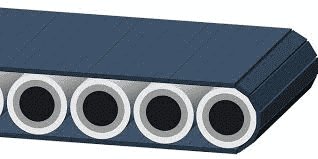
Basic Conveyor System
Design and Design Parameters
The conveyor system design is designed with the below-mentioned components and those are:
Belting – This is the component which is standardized by the industry manufacturers or design based on the requirements provided by the leader and corresponding competition. The mobile belt conveyor system which is present in the plant can also be overheated to line up with the belts used for huge conveyors. This minimizes the modifications that should be piled for emergency substitution.
Idlers – The fundamental idler components which are taken into consideration are shaft and bearing size, and idler rolling wall width, and these all are standardized as well. There even exists considerable dimensional commonality.
Accessories – The other things that are standardized in the conveyor system are protection equipment, plows, zero-speed switches, guards, and scrapers. These can be individually bought from the equipment sellers.
Pulleys – The general type of conveyor pulley is the basic welded kind of steel pulley where it is designed in multiple sizes. The dimensions and sizes for this pulley are mainly standardized by American Standard Welded Steel Conveyor Pulley and it determines few guidelines.
Chutes, Skirting, and idler Stringers – Along with the accessories, these skirting, chutes, and idler stringers are the equipment that has standard designs and designs which are more crucial for the design of conveyor systems. The inclusion of these things reduces the requirement of additional construction on every project.
These are the standardized components used in the conveyor system and those which are non-standardized are:
Drivers
- A conveyor which is above 60 inches in width
- A conveyor which is below 24 inches in width
- While designing the conveyor system, the parameters that are taken into consideration are
- The ideal time (which means system design for continuous material flow) has to be very minimal
- Choose the equipment which has minimal investment and flexibility to manage
- Integration of gravity flow in the system flow
- The ratio in between the material’s dead weight and payload should be very less
And also, the observable things in the design are:
- Idler spacing
- Controlling
- Diameter of the pulley and roller
- Dimensions of the belt, its capacity, and speed
Conveyor Belt System Working Principle
In general, conveyor systems are included with a belt that is stretched over 2 or more pulleys. As the belt surrounds the pulleys, it forms a closed ring so that the pulleys will be continually rotated in the loop. One of these pulleys is termed a drive pulley which pulls the belt and moves the items between different locations.
Many of the conveyor system designs consist of a rotor where this supplied power to the belt and drive pulley. The belt has a continuous attachment to the rotor through the fiction which exists between both surfaces. For the efficient movement of the belt, the idler and drive pulley should function in similar directions which means either both operate in clockwise or anticlockwise directions.
Whereas in the case of some conveyor systems like movable walkways and grocery store conveyor systems, these are straight, and the sections have to be turned for delivery of items to the specified location. To these turns, they have cone shape of wheels or rotors where these wheels allow the system to turn or bend without tangling. This is the basic working principle.
Automatic Conveyor Belt Cleaning System
In automatic conveyor belt systems, carryback is the substance that collects and connects to the belt and this is the major issue in the device. Along with the required regular maintenance activities, the carryback can impose early wear and lethargy on the system components, and this leads to performance difficulties. This can be solved by the integration of belt cleaner in the system, and it solves the issues. The advantages of an automatic conveyor belt cleaning system are:
Enhanced Profitability – Elimination of carryback in the belt system minimizes cleanup and reduces maintenance cost too where ultimately it results in enhanced profitability.
Increased Equipment Durability – Carryback usually piles up under the belt or internal to the conveyor system where might lead to the destruction of internal devices like idlers and rollers and makes damage to the belts. Maintaining belts as clean will protect the conveyor system from the early aging of devices and increases the durability of system components.
Ensures Protection for Employees – When carryback gets accumulated under the belt, it creates damage to the employees where they might slip and fall down when they walk across the material. Even it releases dust which can cause other diseases when inhaled. So, the conveyor belt cleaning approach reduces this issue.
A few of the cleaning approaches are:
- Steam Cleaner – This method generates the dry type of steam vapor where it breaks down the piled-up carryback and cleans the belt.
- Vacuum – This removes the accrued carryback material and then drys out the belt surface.
Types
As there are multiple benefits offered by conveyor systems in numerous domains, there are various types of conveyor system which can be selected based on the requirement and application. A few of the types are:
Auto Kinetics Conveyor Systems
This type of conveyor system provides inexpensive replacements for the general type of welded steel conveyors. The components such as T-section, squeezed out the aluminum frame, and screws on the components allow for system durability, efficient and these can be simply configured in the selected domains. The standard specifications in the auto kinetics conveyor systems are:
- It has 16 gauge stainless steel wear surface
- All the pulleys are coated with ball bearings
- The Center drive section can be placed at any location on the conveyor system
- The customizations for the following sections can be done for this type of conveyor system
- Indexing/dual belt conveyors
- Pallet processing methods
- Timing belt/backlit conveyors
- End and midway stops
Baggage Type of Systems
These are mainly termed baggage handling conveyor systems which are generally used in airports for transporting luggage from ticket allotment counters to the locations where bags are loaded into planes. These are also used for the transportation of luggage from one plane to another plane.
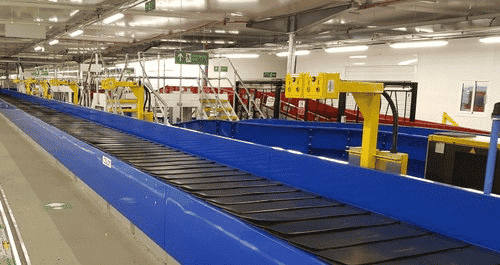
Baggage Conveyor Belt System
The other primary functionalities of BHS along with luggage transportation are:
- Finding any bag jams
- Volume regulation means that input points are managed to prevent overloading of systems
- Load stability ensures even distribution of luggage between the conveyor sub-systems
- Baggage counting
- Luggage tracking
- Automatic tag reader
Coal Mine Conveyor Belt Systems
This is the important mining component that will relentlessly be used for the transportation of mining materials. These are used for shipping huge stone materials in the mining domain across tunnels over distances. Let us consider one type of coal mine conveyor system which is elevating type.
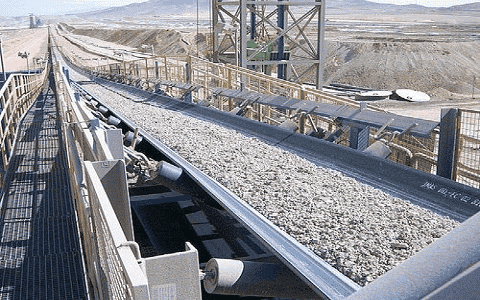
Coal Mine Belt Conveyors
Elevating type of conveyor belt system is usually constructed with belts, tensioning drivers, racks, and rollers. In the process of transportation, this system assists in delivering materials to the specified locations. This type of belt system is mainly used for gradient level shipping means surface mining, underground tunnel mining, and open search in the mining industry. The features of elevating type conveyor system are:
- Better flexibility and good capability
- Increased tensile intensity
- Minimal weight and so maintenance is easy
- Shows good resistance towards longitudinal pulling
- It has good mechanical fastener organizing characteristics
Also, these systems are integrated with intemperate equipment and technology. It provides the options of enhanced performance, good steadfastness and durability, removal of overloading, assembling, and distribution.
Along with the above-mentioned types, the other is:
- Automotive conveyor systems
- Bucket type
- Drag conveyor
- Electric track automobile systems
- Overland conveyors
- Line shaft roller type conveyors
- Pneumatic conveyors
- Auger conveyors
- Vertical type
- Vibrating type conveyor systems
- Wire mesh conveyor systems
Each of these conveyor system types can be customized for every industry with various addons and supplementary equipment to make sure that the system can handle load capacity and move the products between selected locations.
With all this consolidated information, this article also provides a list of few conveyor system manufacturers where this helps people to go through and find the conveyor belt system as per their requirements and specifications.
- Titan conveyors
- Arrowcon conveyors
- Impel intralogistics
- ATS group
- Rich field
- Thomasnet
So, this is the crucial information on conveyor belt systems. This article provides data on conveyor system working, its cleaning methodology, design approach, types, and manufacturers list. In addition to this info, know about how the screw conveyor system is implemented in the conveying process and its working principle?