Well, we are no more in the bewilderment of how metals or thermoplastics are joined or attached, because we live in the era of extensively implementing various welding types. So, welding is one of the most prominent employment that was born several millions of years back. The only welding process that was in evolution until the 19th century was forge welding. The advancements in technology have shown multiple progressions in this welding and allowed us to implement in various industries. We shall now get into the discussion of what are the various welding types and which procedure suits the best for multiple businesses?
What is Welding?
Definition: Welding is considered either sculptural or fabrication methodology which is implemented for the purpose of either thermoplastics or many kinds of metals through heating methods. Heating of metals allows for softening metal components and joining. This is completely different from general kinds of minimal temperature-dependent procedures such as soldering and brazing where these allow for metal softening. With the support of a few tools, welding can be used to transform any kind of metal into desire shape and design.
The advancements in the welding technology have shown us more than 30 welding types ranging from easy oxy-fuel to high-end procedures like a laser beam and robotic welding. The most prominent welding types employed in the industrial procedures are Stick, TIG, MIG, and Flux-Cored welding.
Welding Symbols
Welding symbols are mainly used to establish communication between the welding person and the designer. Welding procedures are classified based on the type of constructional design and the general framework of welding includes a header line that is connected to the arrow, a straight reference line, a weld symbol, and a tail.
- The reference line in the welding symbol is utilized for defining the welding type, location, required proportions, contour, and other additional information.
- The tail is used for indicating the cutting and welding methods along with the welding requirements and necessary operating conditions.
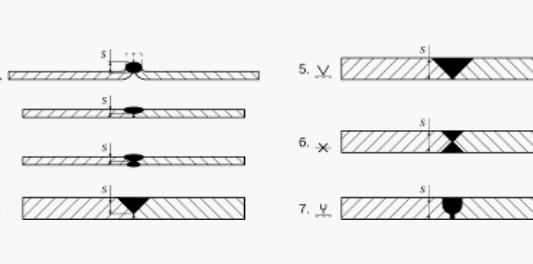
Welding Symbols
Welding Types
This article mainly discusses different types of welding. Based on various parameters like operating conditions, type of gas used, energy source, and other parameters welding type classifications are done.
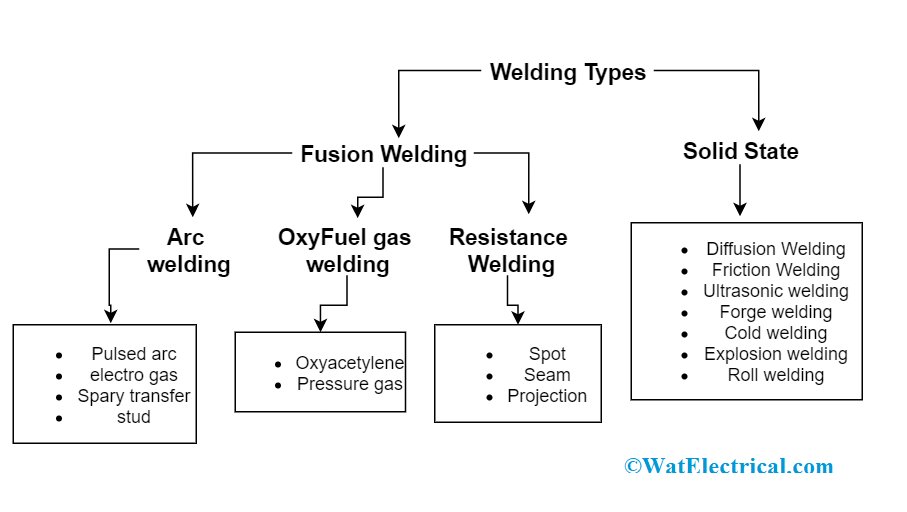
Welding Types
SMAW (Shielded Metal Arc Welding)
It is a kind of welding process where welding is done through a consumable electrode shielded with a flux material. To develop an arc in between the metal and component, the welding machine is attached to the power source that generates an either direct or alternating current. With the formation of arc, melting starts in the metal and electrode thus forming a weld pool. In addition, heat generation will blow off the flux that creates a gaseous surface so as to shield the weld form few atmospheric contaminants and enhances the weld’s quality.
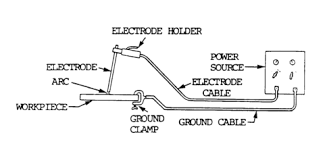
SMAW Welding Type
GTAW (Gas Tungsten Arc Welding)
This welding type is also named TIG (Tungsten Inert Gas welding) which comes under the classification of arc welding that develops the welding joint by making use of a non-expendable tungsten electrode. Mostly used inert gases are either helium or argon because these gases protect from any kind of defects. A plasma column developed of gaseous metals and extreme ionized gas develops energy throughout the arc and is developed by constant welding current source. In this, arc lengths have to be minimal where this avoids the contact between the work and electrode material. GTAW is mostly implemented in the applications where welding slag is not required.
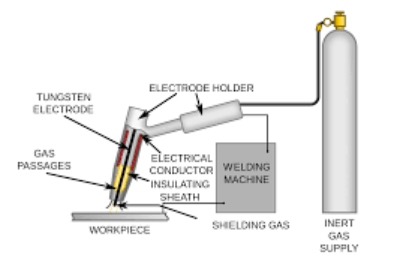
GTAW Type
GMAW (Gas Metal Arc Welding)
This is also termed as metal inert gas welding. Here, a welding location is covered up with the inert atmosphere of either helium, CO2, argon or the composition of these gases. The replaceable wire is fed directly into the welding arc using a wire-feed drive machine via a nozzle. To eliminate oxidation, de-oxidizers are generally used in the electrode metal. The temperatures developed in this welding type is appropriate for thin surface sheets and for the sections having 6 mm thickness. This procedure is employed for welding joints of both non-ferrous and ferrous metals and generally used in the metal manufacturing industry. When compared with the SMAW welding process, this is most adaptable, streamlined, and inexpensive too.
FCAW (Flux-Cored Arc Welding)
Here, an arc is formed between the operating material and the wire electrode. At the time of welding, flux material starts to melt and protects the welding pool from the environment. The power source used in this process is direct current and there exist mainly two variations in this
- Not including of shielding gas
- With shielding gas
The variation that is in between these two is because of various fluxing supporters that exist in the consumables. The fluxing agents help for bot welding pool de-oxidization and protection.
SAW (Submerged Arc Welding)
It is a welding procedure that operates through a usable metallic electrode developing an electric arc in between the electrode and work material inside the coarse protecting flux implemented all across the joint. Welding arc starts to melt both the electrode wire and the working material. The melted electrode substance is then provided across the edges of welded components that fill up the welding pool and combines the working material. Because the electrode is immersed in to the flux material, the arc is not visible. The flux is moderately melting and develops a slag thus safeguarding the weld pool from any kind of oxidation and added atmospheric impurities.
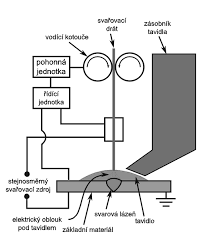
Submerged Arc
Other Welding Types
These are mostly implemented welding types. Besides these, the other industrial welding processes are defined as below:
DB (Diffusion Bonding)
This is the unique solid-state combining process where metals are attached without the requirement of either brazing or cast product formation through resolidification and fluxing. In diffusion bonding, the parameters that show the impact on the relative difficulty of the surface harshness, corresponding metal’s hardness, mechanical properties, and solidifying state of the operating material. The diffusion bonding procedure can be explained through the terminologies of interface movement, diffusion managed mass conveyance, and the microasperity deformation.
Explosion Welding
In this welding type, a welding joint between the metal elements is formed by using an explosive force, and this joint created an electron-distribution metallurgical bond. The welding parameters that need to be considered to create a joint are metallic combinations, metal characteristics, sizes, configurations, and bonding properties of the metals.
USW (Ultrasonic welding)
This method is generally used for thermoplastic infusion molded parts and here mechanical vibrations ahead of the audible range are used. The developed vibrations which are formed either from a horn or welding sonotrode will melt down the thermoplastic material at the welding joint. The components that are utilized here should be maintained under a frequency range of 20 to 40 kHz and imperiled to vibrations.
The capability of the welding joint is based on the parameters of equipment construction, design, and mechanical properties. UW welding type can be done in a very short span of time that is appropriate for the production of mass products. This procedure is implemented in the applications varying from automotive lights to general products like telephone coverings.
ESW (Electro slag) & EGW (Electro gas)
Electro slag welding is the process where it generates extensively productive output. It is mostly suitable for single-pass welding methods where thickness ranges between 25 mm to 300 mm either in the vertical or almost vertical position. The variation that is in EGW and ESW is the initiation of arc in various locations. An electric arc is primarily hit by wire which is directly connected into the required welding part and then after flux is inserted. Extra flux is included when the heated slag reaches the electrode tip.
EGW is termed as the incessant vertical position welding approach where the development of arc happens between work material and the electrode. Here shielding gas is employed but not pressure to develop arc. This is applicable to the development of storage tanks and in shipping industries.
FAQ’s
1). Which type of welding is best?
MIG welding is the most unique and generally implemented type of welding.
2). What is the hardest metal to weld?
Aluminum is considered as the hardest metal as because it is available either in alloy or ore form.
3). Is MIG or TIG stronger?
TIG is the stronger welding method and has enhanced quality too.
4). Do you push or pull a weld?
Pushing a weld corresponds that the welding gun stands behind the weld and forms the bead and pulling a weld corresponds that welding gun stands at the front side of the weld and forms the bead.
5). Why is the gas used in welding?
Shielding gas is used in welding procedures to prevent the attraction of welding pools with the gases present in the atmosphere.
This is all about multiple methodologies in welding Types. There exist various power sources to create welding joints like a laser, gas flicker, ultrasound, electric beam and, electric arc. Precautions and additional care have to be necessary so as to eliminate shock, burns, breathing of dangerous gases, and protection from UV rays. Know more about the concepts of what are welding types and how they are classified?