The concept of welding starts from the ancient time itself where the fundamental process is to join two metal pieces. With the development of technology, there was an enhancement in the welding technologies also. In the initial days of the 19th century, there happened a great revolution in the domain of welding and it was using heat resources for the welding process. Especially, welding technologies gained prominence at the time of welding requirements in World War I and II. And mostly electric arc welding is one of the welding techniques employed in many industries. As the metals in this process are joined using electricity, it was so-called as electric arc welding. So, this article discusses this concept and what are its other concepts?
What is Arc Welding?
Definition: It is a kind of fusion welding procedure where heat necessary to join the metals is received from the electric arc which is placed in between the electrode and the base metal. An electric arc is generated when the two conductors are placed within a distance of 2 – 4mm so that there will be continuity in current flow all the way through the air. Electric arc generates temperature in the range of 40000C to 60000C.
Here, the metal electrode is utilized to supply filler elements and there might be the utilization of either bare or flux coated electrode. Electric arc welding can be done either with AC or DC current supplies. A step-down transformer is used to supply AC current and the generator supplies DC current.
The basic electric arc welding diagram can be represented as follows:
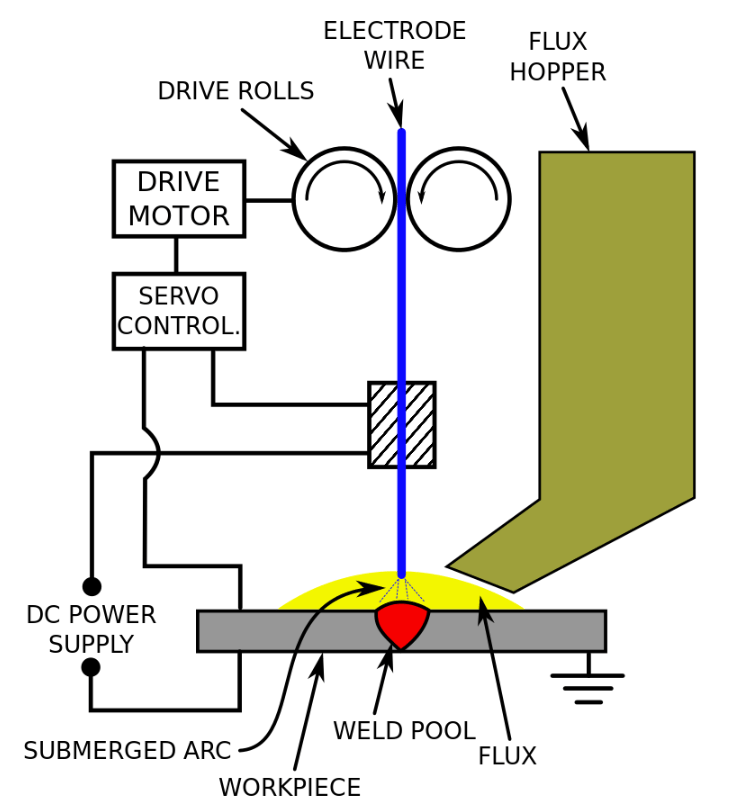
electric-arc-welding
Electric Arc Equipment
To join metals through electric arc welding, the following equipment is necessary.
AC or DC Machine
This welding procedure can be accomplished either with DC or AC electric source. Based on the welding type, voltage ranges between 15 – 45 volts, while the range of current is between 30 – 600 amperes. And the current range is chosen based on material thickness and selected process. In general, sources like motors and heaters operate under constant current and voltages, but in arc welding, these parameters will be varied. The behavior of the welding procedure itself outputs in regular short circuits.
Electrode
This is the filler metal which is employed as terminal in electric current to generate electric arc. This filler metal can be used either in the form of a rod or wire. These electrodes are categorized as non-consumable and consumable. The composition of consumable one is analogous to that of metal and when melted it becomes an element of a weld.
Whereas a non-consumable one can be prepared of either tungsten, carbon or graphite where these materials are not melted during operation.
Chipping Hammer
This tool is used to remove any kind of splatter and slag.
Wire Brush
It is a kind of cleaning equipment that is used to remove waste particles, oxides, and slag.
The other equipment necessary are:
- Earthing clamps
- Cables
- Protecting googles
- Gloves
Principle of Electric Arc Welding
The basic principle of this welding procedure is that an electric arc is generated between the carbon electrode and the metal maintaining at the voltage of nearly 35-40 volts. And in between the metal electrode and the metal voltage is maintained at 15-40 volts. The electric arc that is generated is related to that of heat and bright light all across the length and based on these parameters, arc welding temperature varies in the range of 50000C to that of 55000C.
Process
The electric arc welding process is as below
Here, one side of the electric circuit which is Anode is connected to the work that has to be welded and the other side is connected to the metal electrode where the other side is Cathode. When there is the optimal distance between Anode and Cathode and when there is the circulation of power, there will be the generation of electrons at the side of the cathode. These electrons will have a movement towards the anode, and when there is impingement of electrons on the anode, the kinetic energy is transformed to that of heat energy. So, there happens the generation of heat.
At the same time, there will be positive ion generation at the anode and those have a movement towards the cathode and when there is impingement of positive ions on the cathode, the kinetic energy is transformed into that of heat energy. So, there happens the generation of heat at cathode too.
Types of Arc Welding
As welding is the best approach of joining metals, there are many kinds of electric arc welding. The basic kinds are MIG, TIG and stick weldings.
MIG Welding
This is one of the welding process mostly employed for welding steel. It basically consists of melting a workload with that of a metal. This is termed a fairly tidy procedure where because little amount of waste is produced during welding. Welders can involve in a long time of welding process where just limited stops and starts are necessary. The shielding gas that is used here is either the argon composition consisting of CO2 or O2 or only argon. But the drawback which is in MIG welding is it is somewhat complicated to generate an electric arc and moreover the welds are strongly oxidized.
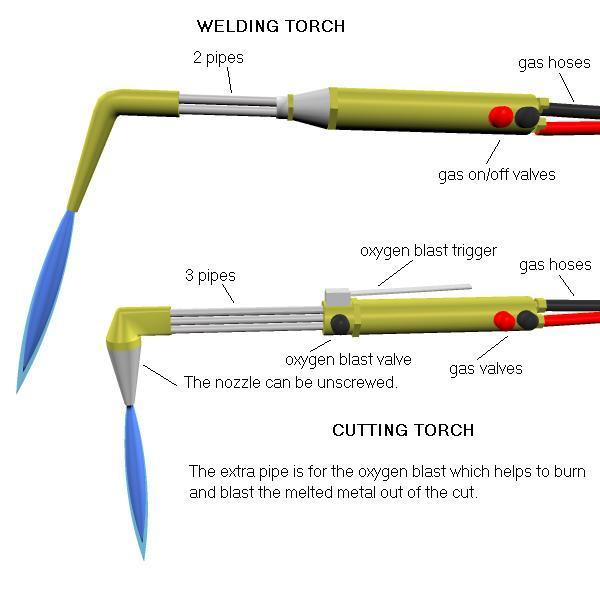
mig-welding
TIG Welding
TIG is also defined as gas tungsten welding, this is the most employed electric arc welding when operating with the alloys such as titanium, magnesium, copper, aluminum, and nickel. This process can be done either in the presence or absence of fill-metals. Welders can be involved only in a smaller period of welding because there will be more amount of heat generation. This is termed a fairly tidy procedure where because little amount of waste is produced during welding. The shielding gas that is used here is either the argon composition consisting of H2 orHe2 or only argon.
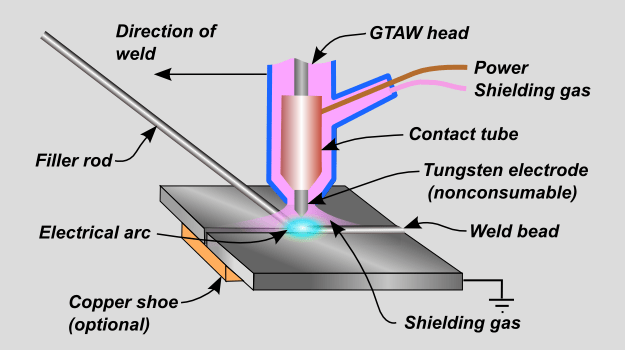
tig welding
Stick Welding
Stick welding is also named as a shielded metal arc. This is employed mostly in the cases of piping, tractors, outdoor, metal arts, and bridges. Mostly outdoor applications will prefer for stick electric arc welding where because rain does not concede the welding integrity. The exact stick welding seems to be complicated and is mostly proposed for highly experienced welders only.
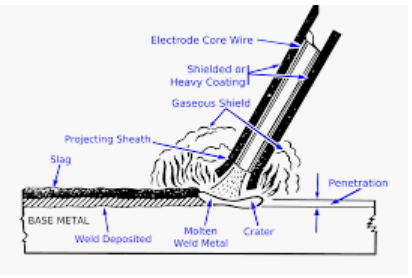
stick-welding
Advantages and Disadvantages
Electric arc welding advantages and disadvantages can be stated as follows:
Advantages
- Electric arc welding has high operating speed along with good welding output
- Easily portable
- This process consists of simple equipment and this makes cost-effective
- It offers consistent welding quality and efficiency
- Provides excellent welding environment
- The power necessary for electric arc generation is not expensive
- The welding joint between the metals is so strong
- It is considered as a fast and stable procedure
- Welders can make use of normal domestic current
Disadvantages
- Mostly highly experienced welders are necessary to perform electric arc welding
- Deposition rate might be imperfect where the electrode coating leads to heat generation and reduce
- Electrode length is nearly 35mm and requires electrode switching for the whole production rate.
Electric Arc Welding Applications
As there are many types of electric arc welding procedures, on the whole, the applications of all these can be stated as:
- Employed in sheet metal welding’s
- In the manufacture of steel and pressure vessels
- Employed in home furnishing and automotive domains
- Used in aerospace and aircraft manufactures
- Used in auto body restorations
- Shipbuilding industries
- Implemented in railroads
- Industrial piping developments
- To weld ferrous, non-ferrous and thin metals
FAQs
1). How hot is a welding arc?
Welding arc heat varies in the range of 30000C to 200000C.
2). How much current is required for arc welding?
In general, the current necessary for welding is 80 amperes and in the case of spot welding, it requires nearly 12,000 amperes.
3). How an electric arc is produced?
The heat necessary for metal welding is generated by an electric arc.
4). How dangerous is welding?
Welding burns when inhaled might cause dangerous health problems. A short period of exposure might cause dry eyes, throat infection. Whereas long period exposure leads to urinary tract problems, lung cancer, and others.
5). What kind of welding is the strongest?
TIG welding is considered as the strongest welding process than compared with that of MIG welding.
So, welding technology is the vast area where the development is ongoing and there come many advancements and trends in this domain. So, get to know what are the other kinds of electric arc welding procedures and how those are employed in industries?