When compared to centrifugal pumps, positive displacement pumps are the most effective ones and screw pumps come under this classification. It came to know that conventional kinds of screw pumps were in availability in the ancient period itself. Then after the screw pump was pioneered by Archimedes. The pumps that were invented initially consists of a cylinder, a revolving unit, and a spiral tube. With the advancements in technology, the operating methodologies of this also got changed and now they are serving wide applications in many industries. So, this article explains the concepts of what is a screw pump, its operating principle and the advantages of this apparatus.
What is a Screw Pump?
Definition: It is considered as the subcategory of a positive displacement pump that operates either with one or more screws to function pump activity in its spindle direction. This pumping machine functions effectively for the liquids which have minimal turbulence, less vibration, self-primed and which hold the ability to function with less air pocket having less functioning noise. The invention of a screw pump has directed to numerous multiple axis machinery where screws revolve in the opposite axis or they continue to be in a static position internal to the cavity.
The cavity might be profiled so that the development of cavities in the pumping equipment will get stuck. Fluid moves into the pump from the suction side and has a linear movement alongside intermeshing screws and from there moves towards the pump discharge side. As the space that exists between the liner and the screws is very minimal, the pressure levels of the liquid are increased at the time of movement.
Screw pumps have various application ranges such as
- Flow rate ranges vary in between 50 – 15,000 per each minute
- Total head ranges vary in between 50 – 4500 psi
- Horsepower ranges vary in between 5 – 5000
Screw Pump Working Principle
The pressure in this is generated through the addition of axial acceleration to the liquid mode internal to the clearance section. The working principle of the screw pump varies completely to that gear pump, here the driver screws and the driver revolves in line by the utilization of timing gear. Both the screws that are functioning through a fine clearance pull in air trapping internal to the fine clearance of interlocking screw strings.
The application of force to the air in the direction of output creates differential pressure that assists to draw in the fluid to pump medium. And now the revolution of shaft pushes liquid towards the outer side because of axial acceleration of the screw movement. The liquid might be trapped either into multiple or one screws based on the pump construction.
The crucial functionality is that the absorbed water moves towards the outer section and then towards the center internal to the pump casing. Through this mechanism, water in all directions moves towards empty space thus invalidating the impacts of directional thrust offering hydraulic stability to the whole pump construction. This working principle shows the effect on pump functionality, output deviations, efficiency and bearing life.
As because of the inclination to produce an extended level of vacuum pressure, this pump does not need any kind of priming and so they are self-primed. In general, screw pumps are operated in the range of 800-2600 rotations per minute. When the shaft’s revolution speed increases, the output flow range will get decreased.
Design
These pumps can be of many types based on the number of screws, constructional change, and percentage share. Irrespective of all these factors, a general screw pump design is constructed with the below parts:
Driver Screw
It is the revolving part of the screw pump that assists in pumping the liquid at the constant volumetric level at any location of the revolution. The crucial functionality of this part is to propel the driven screw through timing gear.
Driven Screw
To make sure of hydraulic stability, both driven and driver screws have opposing directions and this position allows the fluid to move axially to generate the non-pulsating results.
Timing Gear
When the driver and driven screws are unchecked, it might lead to some unexpected situations. In that case, timing gear is installed to verify those kinds of situations. Through timing gear, there will be no metal connection between the driver and driven gears.
Discharge and Suction Ports
These ports provide starting liquid medium to the screw pump thus avoiding the pump from being dried.
Bearings
There are mainly two kinds of bearings:
- Upper bearings which are subjected to heavy loads together with axial and radial pressures at the time of pump operation.
- Lower bearings are subjected to minimal load and they manage an organization of pump components.
Driving Shaft
This portion connects the pump assembly with that of driving motor and this can be achieved by adaptable couplings.
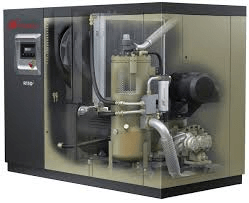
rotary-screw-compressor
Screw Pump Types
Based on various factors, these pumps are essentially classified as five types and they are of:
- One Screw Pump – Also termed as progressive cavity pumps. In general, these are not particularly considered as a screw pump as the rotor is not in the form of a screw but like a crumpled round shaft.
- Two Screw Pump – Also termed as twin-screw pump mostly employed for high range of power applications.
- Three Screw Pump – Here one gear receives power from the source, and this drives the other two gears.
- Four Screw Pump – This is, in general, a two-screw pump having two screws per each rotor. It has timing gears to drive the next one.
- Five Screw Pump – It is similar to that of five screw pumps whereas, in the place of 3 screws, this has 5. A single driving rotor drives all the other four screws.
Screw Pump Applications
- Many hydraulic and lubrication techniques make use of screw pumps to supply lube oil to huge machinery or for the operation of lifts in buildings.
- To pump heavy oils, screw pumps are more helpful. They even hold the ability to pump higher flow and higher viscous liquids.
- These pumping devices are also implemented to pump both gas and liquid at a time, as this is the most critical situation to be handled by many pumping industries, screw pumps handle easily.
- It is also utilized in the industries of oil and gas, mining and manufacturing.
Advantages/Disadvantages
To define there are many screw pump advantages and disadvantages.
Advantages
- These are used in any type of liquid medium
- Most effective to generate non-pulsating and constant results
- It holds the benefit to provide steady flow with varying back force
- The pump is completely noise-free also at extended pressure and rpm levels
- It holds the advantage of generating extended volumetric efficiency
- Regulated output, minimal maintenance and fewer vibrations too
Disadvantages
- Too costly to be implemented in small industries
FAQs
1). Who invented the screw pump?
A screw pump was invented by Archimedes and initially used for irrigation and out ship purposes.
2). How does a screw compressor work?
When the driven and driver gears function in opposite directions, the compressor pulls air in between the space of these gears.
3). How does a twin-screw pump work?
The pump operates in the condition that is transferred to the corresponding volume of fluid based on the pitch and speed of the screws.
4). What is a positive displacement pump?
It has suction and discharge ports where the liquid enters from the suction side when it is expanded and flows out from the discharge side when it is collapsed.
So, this is the concept of what is a screw pump and all other theories of it. There are many other concepts to be known in a screw pump like how they pump fluids, what is a power zone screw pump. Depending on the industry requirement, there are various kinds of screw pumps available in the market. So, choosing the best one yields the best results. Here arises the question is, what happens when screw pumps are maintained properly?