From the past few decades, this closed cycle gas turbine has gained huge prominence because of its crucial involvement in the worldwide energy requirements. In the year 1935, the first patent for closed cycle gas turbines was announced but the commercial usage of these happened in the year 1939. Conventionally, these gas turbines were mostly employed as external combustion engines using brown coal and bituminous coal. But these were supplanted by open cycle gas turbines by making use of light oil or gas oil. With the enhanced performance and availability, these CCGT’s were in high demonstration these days. This article explains what closed cycle gas turbines exactly mean, its working principle, and others.
What is Closed Cycle Gas Turbine?
Closed cycle gas turbine is the turbine which makes use of various gases such as argon, nitrogen, helium, and others as operating fluid as a component of the closed thermodynamic approach. Here, heat is supplied to the system by the other external sources. These systems follow the operation of the Brayton cycle.
In contrast to the open cycle gas turbine, the closed cycle has an internal system where the system pressure is adjusted to change the power output that is released from the turbine. With this, the system holds the possibility to function as a turbine at constant entry temperature to compressor pressure ration so that it maintains better thermal performance even at a minimal range of powers. In particular, the amount of flow rate across the engine is decreased by minimizing the operating pressure because of the blow-off valve opening.
Even though, the off-design efficiency of the engine is enhanced by means of closed cycle gas turbines, the thermal performance of the design point is not high than that of open cycle gas turbines. The causes for the lessening of efficiency are the faults that happen in the heat exchanger. This exchanger does not hold the ability to transfer all the produced hear to the closed cycle gas turbine. This is because a little amount of heat is wasted at the exit point of heat exchanger this results in the minimal thermal performance at the design point.
On the other side, the operating pressure of the closed cycle gas turbine is more than that of the atmospheric pressure, which lessens the constructional volume of the equipment and thus balancing the augmented bulk. The rise in the operating pressure also enhances the heat transfer features of the exchanger. In addition, the operating fluid can be either air or other kinds of gaseous substances such as helium and other gases.
Closed Cycle Gas Turbine Working Principle
In the closed cycle gas turbine system, the operating fluid does not come in interaction with that of either atmospheric air or other gaseous substances used. At point ‘A’, the cold gas which is present undergoes compression in the compressor at the detriment of compressor operation which is Wc. The heat which is necessary for the compressed gas is implicitly provided in the exchanger and this is termed as the source. At point ‘C’, the hot gases operating at increased pressure enters into the turbine. From the turbine, these gases move up to the compressor’s inlet pressure. At the time of gas expansion, the work that is produced is represented as WT.
From the generated work, some amount will be implemented for propelling the compressor and the entire work (WT – Wc) is known as the shaft work. At point ‘D’, dissipating gases of the turbine get cooled in the exchanger by eliminating heat to the cooling system. Now, gas will move again to the first stage. In this process, the same operating fluid which is used in the system gets circulated again and stays unpolluted by the ignition of products. The closed-cycle gas turbine diagram is shown as below:
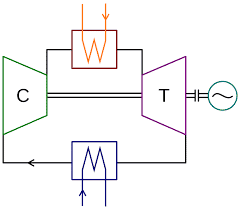
Closed Cycle Gas Turbine Construction
This is the closed cycle gas turbine working.
Types
Various types of CC gas turbine are:
Initially, the closed cycle is categorized as
- Working fluid
- Heat source
In the working fluid type, the gases can be
- Air
- Nitrogen
- Helium along with other noble gases
- S-Co2
Whereas in the heat source type, they are classified as:
- Solar
- Nuclear
- Fossil
- Biomass
And in the nuclear type, there are gas-cooled reactors and LWR, LMFBR. Again, gas-cooled reactors are divided into Indirect and direct cycles.
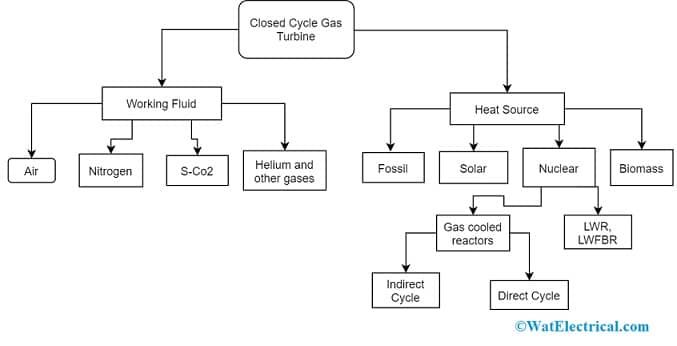
CC Gas Turbine Types
Difference between Open Cycle and Closed Cycle Gas Turbines
Closed Cycle | Open Cycle |
In the heating chamber, compressed air gets heated | In the combustion chamber, compressed air gets heated |
There will be continuous circulation of the operating fluid | Here, there will continual substitution of the operating fluid |
From the turbine, gases are passed into the cooling compartment | From the turbine, gases are depleted into the atmosphere |
Fluids those have enhanced thermodynamic properties can be employed in this system | Here, the operating fluid is the only air |
Maintenance expense is more | Maintenance expense is minimal compared to that of CC gas turbine |
The amount of installation required for kilowatt is more | The amount of installation required for kilowatt is minimal |
In this system, the gases are heated using other sources, So throughout the cycle gaseous amount seems to be constant | As the ignition products get combined with the heated air, so gas will not be constant throughout the cycle |
The turbine blades will not be easily damaged because enclosed gas has no pollution at the time of its flow through the chamber | The turbine blades will be easily damaged because enclosed gas has direct contact with atmospheric air at the time of its flow through the chamber |
Minimal response to the changing load | Shows better response to the changing load |
Increased output | Less output |
There will be a requirement of the huge amount of cooling water | No need for cooling water in this system |
Advantages
The closed-cycle gas turbine advantages are explained as follows:
- In this approach, any kind of fuel like nuclear, solar, gas, or coal energy can be used because heat supply to the operating fluid is from the external source.
- Operating fluids which have better desirable features than that of air like argon, helium those have increased heat levels can be used here. This minimizes the huge amount of flow rate for a similar amount of output power. As a result of this, the constructional size of the system also gets decreased
- The operating fluid is unpolluted and this makes turbine blades and compressor to be not easily damaged
- The CG turbine might be under pressure to decrease the size of the component for the provided amount of gas flow rate
- It delivers enhanced efficiency and output
- Here, there will be no requirement of internal cleaning
- A closed-cycle gas turbine can be constructed using a compressor, chamber turbine, and combustion. This shows the simplicity of the approach
Disadvantages
Few of the closed cycle gas turbine disadvantages are as below
- It requires an external furnace for the procedure of ignition
- The system is expensive and somewhat complicated too
- The closed-cycle gas turbine needs to be strong to withstand enhanced pressures
- It requires coolant for the purpose of pre-cooling
- Any change in the efficiency and performance of the turbine and compressor results in lowering the entire closed cycle gas turbine efficiency
- Here huge air heater is necessary for the operation of the system
Closed Cycle Gas Turbine Applications
- Actively implemented in nuclear power generation systems
- Serves as a power conservation system for many energy sources like solar, biomass, nuclear and many others
Know more about Nuclear Power Plant MCQs.
This is all about the theory of a closed-cycle gas turbines. This article explained clearly on its definition, how the system is operated, its advantages and disadvantages, and applications. In addition, it is also more important to know about what is the closed cycle gas turbine efficiency?