In the industrial domain progression, motors hold a very crucial role and their application is enhancing day-by-day. Not only in the power industries, but in many control applications, motors are playing a critical role. With the enhancement of motor control, the usage and implementation also augment every year. So, the stepper motor is a kind of control motor which operates on positioning control having no feedback loop. Stepper motors were formed at the time of electromagnets development and plunger pumps. During the time when switchover of the excitation phase was developed through contact points, this stands as model for stepper motor development. Actually, the real application of stepper motor started with a variable reluctance motor implemented by the British Navy. From the many kinds came into existence and the one kind is Permanent Magnet Stepper Motor. So, today our article is on the permanent magnet stepper motor and its related concepts.
Permanent Magnet Stepper Motor Definition
As the name of the motor itself indicates that it includes permanent magnets for the construction of the motor. The design is almost similar to that of stepper motors. These are also called as either tin-can or can-stack motors. The rotor of the motor is axially magnetized which means that it has rotating south and north poles in a parallel direction to a rotor shaft. In general, the step angle of permanent magnet stepper motors is 3.60 and there will be an availability of 1.80 step angle also. To deliver enhanced resolutions, these motors are even functioned in half-step, full-step, and micro-step models. When compared with variable reluctance motors, these have increased torque abilities but functioned at controlled speeds.
Permanent Magnet Stepper Motor Construction
This stator construction of this motor is the same as like single stack type of variable reluctance motor. And the rotor is included with permanent magnet poles which are constructed with steel having increased retentivity and are in the shape of a cylinder. The concentrating windings that are in a diametric position to that of opposite poles are in series connection. This kind of connection creates a two-phase stator winding. The stator teeth are aligned with the rotor poles based on the winding excitation. To create winding for phase ‘A’, the coils ‘AA’ are in series connection. And in the same way, to form phase ‘B’, the coils ‘BB’ are in series connection. The below picture shows the permanent magnet stepper motor diagram
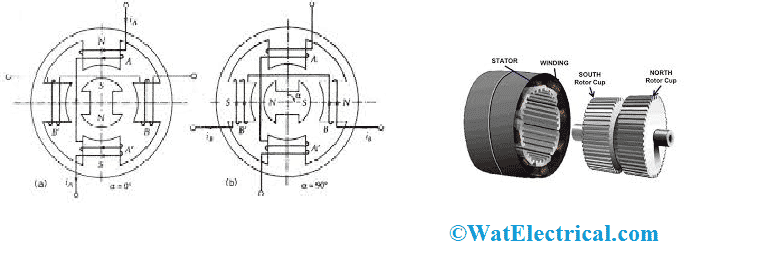
Permanent Magnet Stepper Motor Constructional View
Working Principle
The below theory clearly explains about permanent magnet stepper motor working principle.
From the above diagram, the current movement will be towards phase ‘A’, the phase winding is represented as A+ and current across this winding is iA+. And the phase winding is excited using the iA+ current and the stator phase ‘A’ attracts rotor south pole. So, the stator and rotor magnetic axis will coincide and then α becomes 00.
In the same way, when the current movement will be towards phase ‘B’ end, the phase winding is represented as B+, and current across this winding is iB+. As phase ‘A’ windings hold no current, the phase ‘B’ is excited using the iB+. Here rotor will have a movement of 900 in the clockwise path as the rotor pole is attracted by stator pole and then α becomes 900.
In the next condition when the current flow is from the end towards the starting of phase ‘A’, then the wind and current flow across phase ‘A’ is represented as A- and iA-. The current flows iA- and iA+ are in inverse direction to each other. In this scenario, phase ‘B’ gets de-energized, and phase ‘A’ will be excited through the current flow iA-. So, again rotor will have 900 revolutions in the clockwise path and then α becomes 1800.
Then after, when the current flow is from the end towards the starting of phase ‘B’, then the wind and current flow across phase ‘B’ is represented as B- and iB-. The current flows iB- and iB+ are in inverse direction to each other. In this scenario, phase ‘A’ gets de-energized and phase ‘B’ will be excited through the current flow iB-. So, again rotor will have 900 revolutions in the clockwise path and then α becomes 2700.
So, to have one complete revolution of α = 3600, the rotor again will have a movement of 900 by making phase ‘B’ de-energized and exciting phase ‘A’. So, in permanent magnet stepper motors, the rotation direction is based on the phase current polarity. In the clockwise direction, the rotor sequence is A+, B+, A–, B–, A+, whereas, in a clockwise direction, the rotor sequence is A+, B–, A–, B+, A+.
As it is somewhat complicated to construct large poles in these motors, mostly stepper motors of this type are preferred with a step range from 300 to 900. So, this is the detailed explanation of permanent magnet stepper motor working.
Comparison of Various kinds of Permanent Magnet Stepper Motors
This kind of stepper motors are mostly operated in two-phase having minimal volume and torque and step angle ranges from 3.750, 7.50, 180, and others. The below table shows a clear comparison of various types in this motor.
Type of the motor | Length | Holding Torque measured in (mNm) | Rated Current | Type of the coil | Phase |
8 mm PM stepper motor | 8.5 | 0.4 | 0.25 Amps | Bi-polar | 2 |
10 mm PM stepper motor | 8.8 | 0.5 | 0.2 Amps | Bi-polar | 2 |
20 mm PM stepper motor | 19.3 | 12 | 0.43 Amps | Bi-polar | 2 |
20 mm PM stepper motor | 14.3 | 200 | 0.5 Amps | Bi-polar | 2 |
25 mm PM stepper motor | 17 | 17 | 0.47 Amps | Bi-polar | 2 |
25 mm PM stepper motor | 12.5 | 11 | 0.32 Amps | Bi-polar | 2 |
35 mm PM stepper motor | 21.3 | 42 | 0.63 Amps | Bi-polar | 2 |
42 mm PM stepper motor | 21.3 | 95 | 0.85 Amps | Bi-polar | 2 |
42 mm PM stepper motor | 15.3 | 54 | 0.15 Amps | Bi-polar | 2 |
Advantages
Few of the advantages of the permanent magnet stepper motor are:
- It needs minimal power to operate
- When compared to variable reluctance motor, permanent magnet stepper motor deliver increased detent torque
- There is no requirement of additional circuits for the operation of the rotor
- For each ampere of stator current, high torque is produced
- Shows better response for the operations of stop, start and reverse
- As there exist no contact brushes in this motor, it offers enhanced reliability
- When the windings are excited, the motor will have complete torque at standstill
Disadvantages
Few of the disadvantages of the permanent magnet stepper motor are:
- It has a minimal acceleration
- It shows the very gradual dynamic response
- A reduced ratio of torque to inertia
- Works efficiently when the step angles are in the range of 300 to 900.
Applications of Permanent Magnet Stepper Motor
The applications of this kind of motors are as below:
- Used in computer accessories
- Implemented in photographic and optoelectronic systems
- Used as valve controls
- Employed in ATM and CNC machines
- Used in many automatic winding systems
- Medical instruments and electronic clocks
So, finally, this is all about a permanent magnet stepper motor. As because of many creative benefits, this kind of motor is implemented in many creative applications. The progression of these motors also helps in the development of electronic and industrial domains. Know also on the concepts such as what is the speed-torque performance and efficiency of permanent magnet stepper motors?