Motors are the most crucial development, and they play a wide role in many of the domains like engineering, electrical, and others. As the prominence of controlling motors is enhancing, there come wide variations in motor development such as variation in its speed level, type, and sizes. And the one type of development is stepper motor driver which is a kind o controlling the motor.
The development of stepper motors took place during the period when the plunger pumps and electromagnets happened. Now, this article completely focuses on the concept of the stepper motor driver, its circuit, types, and components.
What is a Stepper Motor Driver?
A stepper motor driver is considered as the driver circuit which facilitates the motor to operate in the method that it works. For instance, these motors need an adequate and regulated amount of energy for phases in the exact order. Because of this, the stepper motor drivers are termed to be more improvised versions of motors than the traditional types of motors.
These devices differ in complexity and modern type of drivers are mixed with a host section of various stepper motor kinds. The configuration of the device is generally done by the user while installing the device. The circuits of stepper motor drivers are available in voltage and current ratings, so it is most crucial to choose an appropriate circuit based on the rating of the motor.
Working Principle
The stepper motor driver working principle is to regulate the functionality of the motor by sending current through multiple phases in the form of pulses in the same direction of the motor. The designers of the device not often utilized the wave driving approach because of the reasons such as minimal torque and inefficiency.
Stepper motor drivers are dependent on the input from an external source for the operation of the device and deliver the output. There will be mainly four signals for the regulation of motor which are:
RESET- Makes the final phase signals be in a specified start point
HALF/FULL – This signal states whether the functionality of the device to be in either full or half-step
CLOCK – This signal provides the stepping control
DIRECTION – It defines the activity of rotation of the motor direction
The power supply to the motor takes place using a microcontroller and this is enough as the drivers require only a few signals for its functionality. The initial signal will be the step signal and the next is the direction signal. When the signal is at +5V, it indicates the direction of the motor, whereas when the signal is at GND level, indicates the motor opposite direction.
A complete step usually requires a couple of rectangular signals in quadrature. Based on the preceding phase, the motor axis will be either in clockwise or anti-clockwise and the rotation is directly proportional to the frequency level of the clock, and this regulates the line pulse. And this is the functionality of a stepper motor driver.
Essential Components of Stepper Motor Driver
The working of stepper motor driver mainly comprises of three components which are
- Controller (essentially a microcontroller or a microprocessor)
- A driver IC to handle the motor current
- A power supply unit
Controller
Choosing a controller for the motor is completely dependent on the initial step of constructing a driver and this should have a minimum of 4 pins which are output pins for the motor. Along with this, it should also consist of an analog to digital converter, serial port and timers, and others based on the usage of the device in which the driver is utilized. The stepper motor driver circuit is shown in the below picture.
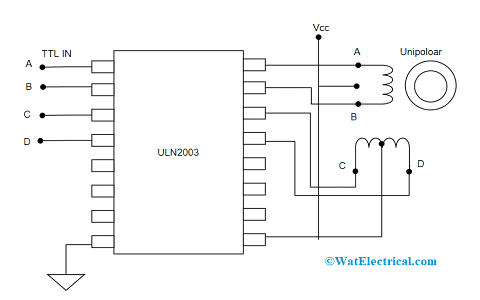
Circuit
Driver IC
These days, apart from using discrete driver elements such as transistors, people are making their move towards small integrated circuits. And these driver integrated circuits are economical and make the implementation process easy while construction enhances the entire circuit design time.
The driver IC’s need to be chosen in order to match with ratings of the motor corresponding to voltages and current values. The most suitable type of driver is the ULN2003 type for stepper motor drivers. Inside the ULN2002 driver IC, each of the Darlington pair can manage nearly 500mAmps and the highest level of voltage that it can handle is 50V of DC.
Power Supply Unit
The stepper motor driver can operate at voltages which are in the range between 5V to 12V and in the same way, the output current lies in the range between 100 Amps to 400 Amps. The specifications of the device will be mentioned by the supplier and based on that specifications, designing should be done. The power has to be controlled so that any kind of instabilities in torque and speed can be regulated.
As this device can operate nearly 1 Amp of current, then the outbound transistor is utilized. It can even handle 5 Amp of current. A proper heat sink section has to be provided based on the entire amount of current that is drawn.
These are the major components in the stepper motor driver.
Types
There are various kinds of stepper motor drivers which have various kinds of features for different applications. The crucial features consist of the input interface and the popular options are mentioned as below:
Step or Directional – The driver alters the output level by transmitting the pulse for the STEP pin. Due to this the motor device performs a step and then the direction of it is known by the point of the DIRECTION pin.
Phase or Enable – For each of the stator winding phases, PHASE defines the current path and then triggers ENABLE only when the phase s energized.
PWM – This type directly regulates the gate signals of both the low and high-sided FETs.
Comprehensive Stepper Motor Drive
This device is a raw type unless the microcontroller is programmed for providing correct signals to the motor device through the driver. And the device can function in multiple modes such as half or full step, and wave drive.
So, it is more crucial to observe the collaboration of the driver to collect commands from customers and perform necessary stepping actions. In addition, the rotational speed has to be controlled and the START/STOP instruction decides to start or stop the rotation of the motor. In order to achieve these functionalities, there have to be more pins for the micro-controller. There is the need for two more pins which are for choosing the stepper motor to START or STOP the device.
And the other is necessary for connecting a port that operates as a speed regulator. The analog to the digital circuit which is internal to the microcontroller is utilized for regulating the rotational speed of the device.
Algorithmic Process
The process is explained in the below steps:
- Start by initializing port pins of both input and output
- Initialize the converter module which is ADC
- Make sure to organize separate operations for half, full stepping’s, wave driver, and relay
- Observe that the two-port pins in order to be in the functional mode and start necessary operation
- Observe the potentiometer reading using the ADC and fix a delay value
- Finish one sequence of cycles and proceed with step 4.
Driver Board of Stepper Motor Driver
When there is a thought of preparing own board by utilizing CAD software such as EAGLE, then it has to be properly observed that the board should be having a good thickness value for the flow of motor current values. Or else, it might lead to overheating.
In addition, as the motor components are inductive in nature, one has to be with utmost care to not interfere with the other signal directions via interferences.
Know more about Electrical Drive MCQs.
Know more about DC to DC Converter.
This is all about Stepper Motor Driver. This article has provided detailed information on stepper motor driver working, circuit, types, its board, and components. Furthermore, know what are the crucial applications of a stepper motor driver?