As we all know that the main functionality of any motor is to convert electrical energy to mechanical energy, speed, and torque. So, the exceptional feature of stepper motors is they hold the ability to precisely managing control related to functional angle and speed. Let’s start with the concept of the stepper motor and then move ahead to know about the hybrid stepper motor. So, a stepper motor which is also termed as stepping motor comes under the classification of a brushless electric motor which partitions a complete rotation into equal phases. So that position of the motor can then be instructed to turn and stop at either of the phases having no use of position sensor for the feedback. Now, we shall know about hybrid stepper motors and its related concepts.
Hybrid Stepper Motor Definition
By the combined characteristics of variable reluctance and a permanent magnet, stepper motors are designed. In a similar aspect of permanent magnet motors, hybrid stepper motors also have permanent magnets present in the rotor teeth. The pair of teeth termed as cups circulate the rotor. These are magnetized to create a pair of poles as North and South poles. Also, there are hybrid control kind of stepper motors which deliver augmented performance and response. In addition to the open-loop system, it also provides closed-loop system advantages.
Through this kind of motor, the motor’s position can be continually observed, and then the driver can easily switch in between closed-loop and open lop based on the condition. In general scenarios, the functionality of the motor is observed and the application of control is done similar to a normal stepper motor. When an error arises between the position of motor and command because of heavy load, then the system automatically turns up to a closed-loop like that of a servo motor. This updates to the exact speed level and position thus the required position is maintained.
This is all a basic hybrid stepper motor theory.
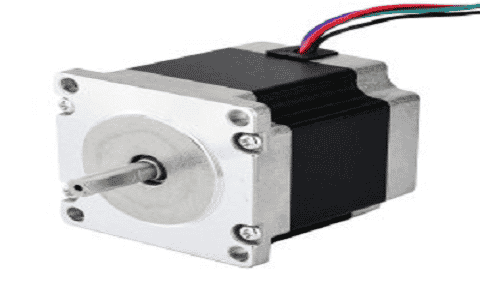
Two-Phase Stepper Motor
Features
A few of the features of the hybrid stepper motor are:
- Simplified control through pulse signals
- Accurate positioning control
- Using small size, high torque values can be generated
- The motor itself has a ceased position
- When there is a power failure, the self-organizing torque of the motor gets failed and the motor will not be at a stopped position in vertical functions or when there is the application of some external force.
Hybrid Stepper Motor Working
Similar to that of VR motors, these hybrid motors also have stator poles and these poles are called teeth. The stator includes 8 poles where each pole has a coil and few teeth say ‘S’. The below theory explains hybrid stepper motor construction and working.
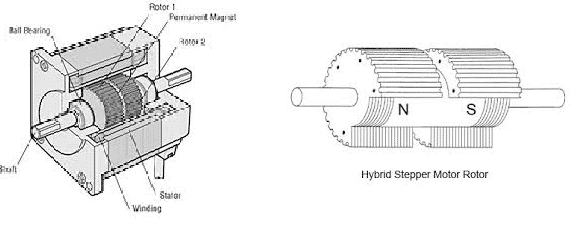
Construction and Working
In general, a stator has 40 poles and every cap has 50 teeth. So, here the count of stator and rotor teeth are 40 and 50 and, in this case, step angle is shown as:
Step Angle = [(50-40)*360]/50*40
= 1.80
Both the stator and rotor teeth are aligned with each other. Both the teeth present at two ends of the cap are dislocated by each other by the way of the center of the pole pitch. As because left and right end caps are axially magnetized, they gain polarities like north and south poles. The coils that are present on 1, 3, 5, and 7 poles have a series connection to create an ‘A’ phase. whereas the coils that are present on 2, 4, 6, and 8 poles have a series connection to create a ‘B’ phase.
In phase ‘A’, when it is excited through the external current, then 1 and 5 poles converts into south poles and 3 and 7 as north poles. Now, when phase ‘A’ has no energy and phase ‘B’ is operated, then the rotor will revolve by a 1.80 step angle. This makes phase ‘A’ as negative energized. In addition, the revolution of the rotor needs phase ‘B’ to be negatively excited. So, to create the anticlockwise movement of the motor, the below order of phase excitations are needed: +A, +B, -A, -B, +B, +A. Whereas to create a clockwise movement of the motor, the below order of phase excitations are needed +A, -B, +B, +A. This is the hybrid stepper motor working principle.
Different Types
Few of the types of hybrid stepper motor are:
Brake Type – This kind of hybrid motors is provided with a non-excitation kind of electromagnetic brake. When there is a sudden power failure, the brake keeps the load in position so that it eliminates any kind of dropping. These are mostly implemented for vertical axis purposes.
Geared Type – This kind of hybrid motors are provided with a strong position managed gearhead having minimal backlash which has increased motor controllability. This gearhead makes sure of enhanced accuracy, and soft functional flow even they receive a large amount of torque.
IP65 – These kinds of motors having the characteristics of resilient to minimal pressure water jets and dustproof are mainly suitable for the applications in damp situations like the beverage and food industries. These motors stipulate a product that has no dust entrance and enhanced safety against water jets.
The other types of hybrid stepper motors are:
- Encoder type
- Basic type
- Integrated-type having a controller and drive
Comparison of Hybrid Stepper Motor with other Motors
- Hybrid motors have a minimal step angle of 1.80 when compared with variable reluctance or permanent magnet stepper motors
- It has increased output torque whereas for variable reluctance motors it is low and for permanent magnets it is moderate
- The pulse rate and speed of hybrid stepper motors and variable reluctance motors are high
- Hybrid stepper motors have quick acceleration and response
- It produces quite less noise when compared with variable reluctance motors
Advantages
Few of the hybrid stepper motor advantages are stated as below:
- Each step which occurred in the motor is minimal
- It delivers increased torque
- The motor offers high detent torque having de-energized windings
- It functions with increased performance even at minimal speeds
- Minimal stepping rate
Disadvantages
Few of the hybrid stepper motor disadvantages are stated as below:
- The inertia of the motor is more
- The design, weight, and construction of the motor is complicated due to the existence of rotor magnet in it
- The reliability and the efficiency of the motor gets disturbed when the magnetic strength is altered
- When compared with variable reluctance motor, hybrid stepper motors are somewhat economical.
Applications
The hybrid stepper motor applications are
- Hybrid stepper motors will be suited for the applications that need a quiet and smooth operation
- Applied in motion control positioning systems
- Computer and 3D printers
- Camera lenses
- Image scanners
- Floppy disk drives
Know more about Switch Gear and Protection MCQs.
Know more about Variable Reluctance Stepper Motor.
This is all about the detailed concept of hybrid stepper motors, how they are constructed, their working principle and advantages. As because of accurate positioning and other benefits, these motors are widely employed for many industrial applications. Also, know more about the related concepts such as hybrid stepper motor diagram and commercial applications?