The history of the turbo generators dates back to late 1800s when Charles Algernon Parson developed the first steam turbine which uses high pressure stream to rotate a shaft that was connected to the generator. In simple terms, the first turbo-generator is an electrical generatorthat was powered by water turbines. The breakthrough allowed for much more efficient generate of electricity compared to the traditional steam engines which were bulky and had limited output.
Parson continued to refine his steam turbine design and the first large industrial AC turbo generator with megawatt power was supplied to a power plant in the year 1901 in Eberfeld, Germany. His innovation helped spur the growth of the power industry and led to the development of the large scale power plant. Modern day turbo generators use a variety of fuels, including coal, natural gas and nuclear energy, to produce electricity on a massive scale. They are essential to the operation of the power plants around the world to provide reliable and affordable electricity to million of people.
This article provides brief information on a turbo generator – working with advantages & its applications.
What is a Turbo Generator?
An electric generator that is used to generate electric power by converting mechanical energy to electrical energy by connecting to the shaft of a gas/ steam turbine is known as a turbo generator. It is also called as Turbo Alternator. These generators are designed in different sizes & shapes to meet many residential & industrial requirements. These generators can also be arranged to run off of steam, electricity & several different biofuels. The turbo generator with large steam power provides more electricity around the world used by turbo-electric ships powered by steam. Small turbo-generators driven through gas turbines are frequently utilized as auxiliary power units. The diagram of the Turbo generator is shown below.
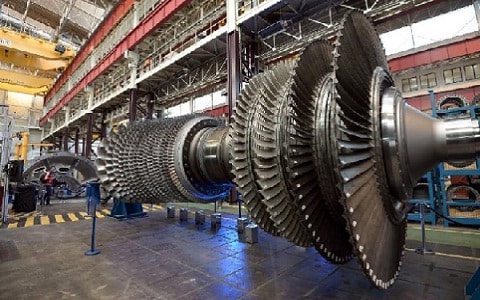
Turbo Generator
Specifications
The specifications of the turbo generator include the following.
- The ambient temperature ranges from -15 to 40°C.
- The altitude is 1,000 m or below.
- Humidity is 90% or less.
- Types of ratings are continuous.
- Output ranges from 5,000 kVA- 45,000 kVA.
- Voltage is 6,600V or 11,000V or 13,800V.
- The power factor is 90% (lagging).
- The frequency is 50Hz or 60Hz.
- The number of poles – is 4.
- Applicable standards are JEC2130 or IEC60034.
- The protection degree is IP44.
- The cooling system type is IC8A1W7.
- The thermal class is 155(F).
- The rise limit of temperature is 155(F).
- The rotor type is Cylindrical.
- Force lubrication system.
- Double-bearing support system.
- The excitation system is a brushless type including PMG (permanent magnet generator).
Turbo Generator Construction
The turbo generator is constructed with different components. So the turbo generator parts mainly include the stator, stator frame, stator core, stator winding, bushing, excitation system, cooling system, rotor, rotor shaft, rotor winding, retaining ring, rotor wedges & rotor fan.
Stator
The inactive part of the generator is known as a stator where the stator body is totally enclosed by gas. The stator is designed with mild steel & high-quality austenitic steel.
Stator Core
The stator core of a generator has a thin lamination which is made with a no. of the individual segment. Here, these laminations are helpful in reducing eddy current. So the stator core’s main features are; they carry magnetic flux efficiently & provide mechanical support.
Stator Frame
The stator frame in this generator is very is the heaviest part which is utilized for decreasing vibration and also to bear the gas thermal pressure.
Stator Winding
Stator winding includes 3-phases & double layer winding through a pitch so that we can decrease the fifth and seventh harmonics.
Rotor Shaft
The rotor shaft is a solid single piece, designed from vacuum cast steel where the slots are arranged on it. The rotor body edge is provided with 60% of longitudinal slots with field winding.
Bushing
Bushings are very helpful in separating the 3-phase winding’s opening & endings from the stator frame to provide higher voltage insulation. So these bushings are simply connected to the stator frame at the exciter’s end.
Rotor Wedges
The rotor in this generator is useful for protecting the winding from the effects of centrifugal force & they are protected through rotor slot wedges. So these wedges are made with a copper alloy.
Rotor Fan
In this generator, the cooling air is dispersed by axial fans which are arranged on the rotor’s shaft. For example, on both the end of exciter & turbine in the 220 MW type of rotor, two axial flow fans are used.
Excitation System
The process of magnetic field generation with an electric current is known as excitation. Generally, a Turbogenerator is an exciting machine that provides the suitable DC field current to the field winding constantly.
Brushless Exciter
This exciter has two main parts such as; a three-phase main exciter and a permanent magnetic pilot exciter.
Cooling System
In the turbo generator, the cooling system plays a key role because it dissolves the produced heat by different losses and also expands the life of the insulating material. The cooling system is normally divided into three main parts; air cooling, hydrogen, and water cooling.
Working Principle
The turbo generator simply works on the principle of electromagnetic induction. So when this turbo is attached to the electrical generator then the kinetic energy of the steam stops the fan blades of the turbo & the generator’s rotor revolves to produce electricity. In this generator, both a turbine with a generator together can change the moving fluid’s mechanical energy like water, natural gas, air, or steam into electrical energy. Turbines significantly change based on their application and they can be utilized to harness the power.
Generally, the turbogenerator speed is 1500 rpm/3000 rpm with a minimum of 2 or 4 poles at 50 Hz frequency & speed of 1800 rpm/3600 rpm with 2 or 4 poles at 60 Hz frequency. This generator’s rotating parts can cause high mechanical pressures because of the higher operating speed. The rotor in these generators is normally forged with solid steel & alloys to make the rotor resistant automatically.
Types of Turbo Generator
There are different types of Turbo generators available which are discussed below.
- Air-cooled Turbo Generator
- Hydrogen-cooled Turbo Generator
- Water-cooled Turbo Generator
Air-cooled Turbo Generator
The air-cooled generators are consistent, strong & very simple to maintain. These generators need few auxiliaries to work & this decrease the early investments to understand the plant. These types of turbo generators are simply used with steam & gas turbines within single/multi-shaft arrangements. These are also utilized in geothermal applications, wherever the conditions of the environment are mainly severe.
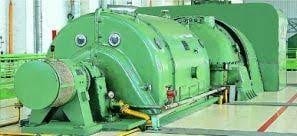
Air Cooled Turbo Generator
Air-cooled turbogenerators include directly-cooled rotor & indirectly-cooled stator windings. These are self-ventilated within a closed circuit through air-to-water coolers. Specific solutions provide the option to work in high over-pressure to let for further power extensions, otherwise through light overpressure to set up and work the generator in dangerous areas.
Hydrogen-cooled Turbo Generator
A hydrogen-cooled turbo generator is used with steam & gas turbines within a single/multi-shaft arrangement. These generators are reliable, easy to maintain & robust. Hydrogen in this generator simply increases overall performance & provides low frictional losses. These turbo generators have high thermal and hydrogen gas properties, so these are most frequently utilized in different fields.
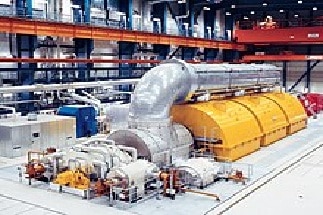
Hydrogen Cooled
The Hydrogen cooled turbogenerator features mainly include high performance & long life. There are different turbo generator models available in the market such as good quality, high efficiency & optimum reliability which are hermetically sealed to keep away from the leakage of hydrogen gas.
Water-cooled Turbo Generator
Water-cooled turbo generators are designed with water-cooled stators & hydrogen-cooled rotors which are high-range machines used in very high-power turbines. These turbo generators have high quality, efficiency, and optimum & reliable operation.
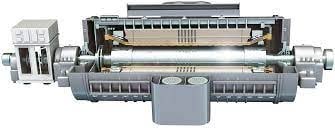
Water Cooled Turbo Generator
Water-cooled Turbogenerators are utilized in large power plants because of their solid design. These generators follow ATEX and PED regulations to give secure operation once hydrogen gas is obtainable. These generators with water-cooled stator windings are fixed by laminated press plates to decrease further losses & also to eliminate hotspots.
Advantages
The advantages of turbo generators include the following.
- Turbo generator has many benefits like high reliability, high control response, long life, high efficiency, etc.
- This generator doesn’t depend on the temperature of the atmosphere.
- It is very simple to use with an accessible rig.
- It is very simple to design.
- These are economical as compared to other generators.
Disadvantages
The disadvantages of turbo generators include the following.
- A Turbo generator is a high voltage machine so there is a chance to occur a spark within an air & electric shock through contact.
- Its cost of repair is high.
- Its maintenance cost is high.
- This generator has small components.
- It is available in big sizes and is heavyweight.
- These are expensive.
- It uses a very low speed of air to delay the performance.
Applications
The applications of turbo generators include the following.
- This generator is used to generate electric power by connecting it to the shaft of a turbine.
- These generators are mainly used for maximum shaft rotational speeds in gas & steam turbines
- This is used to change the mechanical energy of a moving fluid like steam, liquid water, air, or natural gas into electricity.
- It is used on steam locomotives as a power source for water pumps & coach lighting used especially for heating systems
- This is an engine-driven alternator that uses diesel fuel for driving the engine correctly on-site.
- These are normally used wherever standby & emergency power is required when utility power fails like hospitals.
- This generator with large steam generates electricity.
- These are used with turbiditic vessels which are operated by the current.
- These are utilized like auxiliary power supply units.
- These are used in different power plants like thermal power plants, hydropower plants & solar power plants.
Which Type of Rotor is best for a Turbo Alternator?
For a turbo alternator or high-speed alternator, a smooth cylindrical type rotor is normally used because; these rotors have long axial lengths & small diameters which allows them to rotate with high speeds which range from 1500 rpm – 3000 rpm.
Which Type of Generator is used in Thermal Power Plants?
A steam turbine-driven generator or turbo generator is normally used in a thermal electric power plant.
What are the Methods of Loading Turbo Generators?
A turbo generator is loaded with a single method by simply connecting a generator to the expansion turbine’s shaft.
What is the Function of a Turbo Generator?
A turbo generator’s function is to generate electric power by connecting to the shaft of a gas/steam turbine.
What Is Turbo Generator on Ship?
A Turbine generator is a very popular clean power generation source on ships because they don’t utilize any kind of fuel like diesel oil. These generators with large steam power provide the electricity so these are used by turbo-electric ships powered by steam.
What is the Efficiency of the Turbo Generator?
The efficiency of a Hydrogen-cooled turbo generator is 99.0%. So this is the most common type of turbo generator used today due to its high specific heat, high efficiency, high thermal conductivity & low hydrogen gas density.
Why Do Generators Have Turbos?
A turbo generator with a generator together changes the mechanical energy of a moving fluid, like liquid water, air or natural gas, or steam into electricity.
Thus, this is all about an overview of a turbo generator – working with applications. A Turbo generator is mainly designed to work in the segment of power generation through oil, gas, geothermal & biomass. As these generators are high voltage devices that range from less than 1500V, thus the efficiency of a machine is accurate. So these generators are more reliable in nature. These are used with gas or steam turbines. Here is a question for you, what is the function of a generator?