A variable reluctance stepper motor is electromechanical energy which converts electrical energy to mechanical energy. The main difference between the stepper motor and other DC motors is in stepper motors the motion of the rotor is achieved in steps. Stepper motor also works on DC supply but the principle of operation is not Lorentz force law. It works on the principle of reluctance. That is, the magnetic flux always tries to follow in the least reluctance path. This principle is also true for other reluctance motors such as switched reluctance motor and synchronous reluctance motor. the working of variable reluctance stepper motor depends on the principle of variable reluctance.
What is a Variable Reluctance Stepper Motor?
A variable reluctance stepper motor is an electromechanical energy conversion device that converts electrical energy to mechanical energy. It works on the principle of reluctance, according to which magnetic flux always flows through a minimum reluctance path. The stator poles are excited with three-phase or single-phase supply and the rotor is either made of permanent magnets or excited with single-phase supply to obtain the rotor magnetic field.
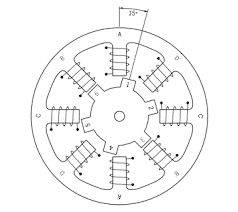
Variable Reluctance Stepper Motor
There are two important features of variable reluctance motor as compared to other reluctance motors. First is, in this case, the reluctance is not constant. It is a variable reluctance. The variable reluctance means the magnitude of the magnetic field is varied to obtain the variable reluctance. One more way of obtaining the variable reluctance is by modifying the air gap between the stator rotor windings. To obtain this, the outer surface of the rotor structure is made of tooth type slots where the windings are placed. The second important difference is in this motor, the rotor rotates not in continuous motion but in steps. The step angle is defined as
Step Angle = (360/m*Nr)
Where m is the number of stator phases and Nr is the number of rotor poles.
Variable Reluctance Stepper Motor Working Principle
Variable reluctance stepper motor works on the principle of variable reluctance. When the stator winding is excited by three-phase or single-phase supply, then it creates a rotating magnetic field around the stator windings. The stator windings are excited by using a switching circuit. The switching circuit consists of an inverter circuit, which converts the DC supply to three-phase AC supply.
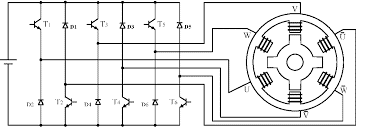
Switched Reluctance Motor Design
As shown in the circuit, the three-phase magnetic field is obtained by connecting the switching circuit to the stator windings. The switching circuit consists of the inverter circuit. An inverter circuit, six devices are connected to the stator poles. The devices used are like MOSFET, IGBT, etc. the devices are numbered as per the sequence of firing. The devices are classified into two groups. Positive group and negative group. In the positive group, we have the devices numbered as (1,3, and 5) and in the negative group, we have the devices numbered as (2,4 and 6). The device, 1, and 2 are connected to one phase of stator windings, let us say R phase. Similarly, device 3 and 4 are connected to phase Y, and 5 are six are connected to B phase.
Now to obtain variable reluctance, the switching circuit is designed such that, first R phase has maximum magnetic energy, then Y phase and then Y phase. So when the R phase has maximum magnetic energy, the rotor will try to align itself into the R phase. After a delay of some time, the maximum energy is shifted to the Y phase. At this time, the rotor position is shifted to the Y phase through a clockwise rotation. The rotation angle of the rotor is defined as the step angle given by Step Angle = (360/m*Nr), where m is the number of phases and Nr is a number of rotor poles. Interestingly, it may be noted that, in this motor, the number of stator and rotor poles need not be the same.
Construction
In variable reluctance stepper motor construction, the stator poles are made of silicon steel. Since the main role of stator poles is to produce a magnetic field, they are made of good magnetic material. The windings are made of copper. The stator windings in the case of three-phase machines are connected in delta or star. The reason for connecting in star or delta is for producing a rotating magnetic field. As per the theorem of rotating magnetic field, whenever three-phase windings are excited with three-phase supply, a rotating magnetic field is created which rotates at synchronous speed.
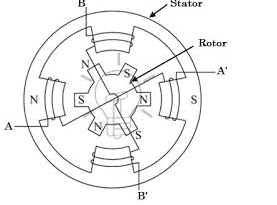
Construction
The rotor windings are made of ferromagnetic material. The ferromagnetic material has the property of least reluctance. Whenever a ferromagnetic material is placed under the influence of the magnetic field, then the magnetic field lines completely pass through the material. No magnetic flux passes through the air. The reason is air has high reluctance as compared to the reluctance of ferromagnetic material. One more good property of ferromagnetic material is it produces the least amount of eddy current and hysteresis losses. Due to the property of ferromagnetic material, the number of magnetic cyclic variations are less due to which the hysteresis losses are less. Similarly, to reduce the eddy current losses, the windings of the rotor are well laminated.
Apart from the stator and rotor structure, the reluctance motor has switching circuits to produce variable reluctance.
Variable Reluctance Stepper Motor Working
Variable reluctance stepper works fundamentally on the principle of variable reluctance. To produce the variable reluctance, a switching circuit is used to excite the stator windings at different phases. The switching circuit consists of an inverter circuit which can produce a variable AC from a fixed DC supply. To obtain the variable magnetic field, the triggering angle of the inverter circuit is varied periodically such that each of the phases of the stator windings is excited with maximum energy at one particular instant.
Generally in an inverter circuit, the delay angle triggering each device is 60 degrees. It can be varied periodically. One more method of obtaining the variable reluctance is by designing the rotor and stator poles such that, air gap among them is varied. Varied in the sense, at one instant, the air gap is maximum and at the other instance, the air gap is minimum. This is obtained by using a toothed type of rotor.
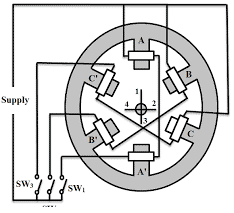
Motor Working
When one phase of the stator has maximum energy, the rotor is aligned to that stator at that moment. As we discussed it follows the reluctance principle. As per the reluctance principle, the magnetic flux flows through the minimum reluctance path. Just like the current flows through the minimum resistance path. The reluctance is the magnetic equivalent of resistance and flux is the magnetic equivalent of current. So when one phase of the stator has maximum energy, the rotor is aligned to it.
Once the energy is shifted, by using the switching circuit, the rotor also shifts its position to the new phase where reluctance is minimum. The angle by which it rotates is called a step angle. It is defined as Step Angle = (360/m*Nr), where m is the number of phases and Nr is a number of rotor poles. For six poles, 4 phase the step angle would be approximately 15 degrees. It can be noted that the step angle for a particular machine is fixed, as we can’t vary the number of phases or number of rotor poles.
Advantages
The advantages of variable reluctance stepper motor include the following
- Its rotation is in stepped form. It is very useful for a particular operation where we don’t need continuous motion.
- Losses are very less as most of the material is made of magnetic material.
- It can run with both AC and DC supply
- Due presence of electronic devices production of variable reluctance is very easy.
Disadvantages of Variable reluctance stepper motor
- Speed control is not possible for this machine, as it rotates in steps.
- For a particular operation, the step size is fixed.
- Due to its step rotation, it has less number of applications
- The electronic devices cause some losses such as switching losses.
Applications
The applications of variable reluctance stepper motor include the following.
As mentioned, due to its stepped rotation it has less number of applications. Mostly these types of motors are used in toys, tape recorders, advanced clocks, printing machines, etc.
Know more about Hybrid Stepper Motor & Difference b/w Motor and Generator.
Hence, this is all about an overview of the variable reluctance stepper motor. We have seen the operation, constructional aspects, and advantages of the stepper motor. By varying the firing angle we can vary different control aspects of the machine. And we can form a closed-loop operation of the motor circuits and using controllers like PID, space vector controller, etc. It is interesting to think in variable reluctance stepper motor, is it possible to obtain the rotation of the rotor in both clockwise and counterclockwise direction?