Synchronous reluctance motor is an electromechanical energy conversion device that converts electrical energy to mechanical energy. Unlike DC motor which works on Lorentz force law, synchronous reluctance motor works on the variable reluctance principle. The main characteristic of this motor is, it runs at synchronous speed. Due to magnetic locking, it follows the synchronous speed of the rotating magnetic field which is formed
at stator poles. Due to its constant speed, the motor has few applications as compared to switched reluctance motor. One more disadvantage with this device, speed control is not possible, as the rotor is always locked to the stator magnetic field.
What is a Synchronous Reluctance Motor?
Synchronous reluctance motor is an electromechanical energy conversion device, which converts electrical energy to mechanical energy. The motor always runs at synchronous speed due to magnetic locking between the rotor magnetic field and the stator magnetic field. In a DC motor, the torque is produced due to interactions between stator and rotor magnetic fields, which is also knowns as Lorentz force law.
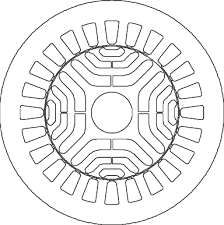
Synchronous Reluctance Motor
But in synchronous reluctance motor, it follows the reluctance principle. Constant reluctance torque is produced in the rotor which causes the motor to run. It may be noted that in switched reluctance motor, a variable reluctance torque is produced, which is produced because of switching circuits. Switching circuits produce a rotating magnetic field at the stator. But in synchronous switching circuits are not required as we are not going to vary the speed of the motor.
Synchronous Reluctance Motor Principle
The fundamental concept behind the operation of this motor is the reluctance principle. When a ferromagnetic material is placed under the influence of the magnetic field, the magnetic lines flow through the material avoiding the path outside or surrounding the material. Since in the surrounding, the air is present and air has high reluctance as compared or reluctance of the materials. Reluctance is equivalent to resistance in the magnetic field. As we know that, the current always try to flow in the least resistance path, similarly, the flow of magnetic lines which is also called flux lines, try to flow in the least reluctance path.
When the stator is supplied with 3 phase supply, the stator windings which are placed in star or delta configuration, produce a rotating magnetic field. The reason for the production of rotating magnetic field is as per theorem of rotating magnetic field according to which, whenever a three-phase winding is supplied excited with a three-phase supply then it produces a rotating magnetic field which rotates at a speed of synchronous speed given by (120*f/P), where f is the frequency and P is the number of poles. For a six-pole machine, the magnetic field rotates at 1000 RPM.
The rotating magnetic field, when crosses the air gap and interacts with rotor windings, the rotor winding tends to attract the stator magnetic field.It must be noted that the rotor is mostly of squirrel cage type like in an induction motor. But whereas in a synchronous motor, the rotor is of a salient pole of the cylindrical structure. When the rotor winding is cut by the stator magnetic field, they too produce a rotating magnetic field and based on reluctance principle, try to align with the stator magnetic field. Since the stator magnetic field is rotating at synchronous speed, the rotor also starts rotating at synchronous speed due to magnetic locking between the stator and rotor magnetic field.
Please refer to this link to know more about Synchronous Motor MCQs
Phasor Diagram
One important characteristic of synchronous reluctance motor is its constant speed. At the start, if the rotor fails to align with the stator magnetic field, in that case, damper winding comes into the picture. They are also used in synchronous motors. The damper windings which are placed in pole shoes, produce damping torque due to relative speed difference between the rotor magnetic field, and the stator magnetic field.
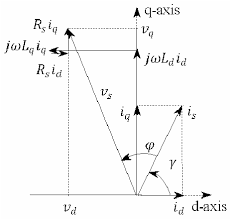
Phasor Diagram
This happens when the rotor fails to align with the stator. The damping torque produced, according to Lenz Law tries to oppose the reason for its production, which is the speed difference between rotor and stator magnetic field. Hence the damping torque pushes the rotor winding such that it gets magnetically locked with stator magnetic field. And afterward, the rotor runs on synchronous speed for the remaining time. The synchronous reluctance motor phasor diagram is shown above. The q axis and d axis are defined based on the two-axis theory of synchronous machine. Similarly, we can define Vd and Vq, which are the voltage across the d and q axis. Gamma is the angle between d-axis and stator current Is. This is also defined as a rotor angle. The synchronous torque produced is a function of the rotor angle.
Construction
Constructional features mainly include stator and rotor windings. The stator winding is of three phases in nature. Which means that they are connected in star or delta. The reason for this, when they are excited with a three-phase supply, they must produce a rotating magnetic field. The stator winding is made of silicon steel stampings.
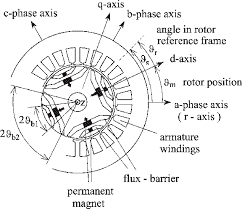
Synchronous Motor Construction
The rotor windings are made up of ferromagnetic material. The reason for this, since the rotor, has to align with stator magnetic material as per reluctance principle, therefore the reluctance of the rotor windings must be least. As shown in the figure, the armature windings are placed on the stator and the field winding is placed on the rotor. It is just the opposite of the DC generator. The reason is mainly due to insulation problems, and since the armature windings carry the armature currents, it is better to keep them static. The stator winding is excited with a three-phase supply as shown in the figure. In low rating machines, permanent magnets are used for rotor windings. They don’t need any separate excitation.
Synchronous Reluctance Motor Working
When the stator windings are excited with a three-phase supply, they produce a rotating magnetic field in the stator windings. The magnetic field rotates at a synchronous speed based on the number of poles and frequency. The fundamental concept behind the reluctance motor is the reluctance principle. The rotor windings are of squirrel cage in shape just like in induction motor. When the rotor windings are excited with DC supply, they produce a magnetic field at rotor windings. Now we have two magnetic fields, one is the stator magnetic field and the other one is the rotor magnetic field. The stator magnetic field is rotating at a speed of synchronous speed.
Now the rotor windings are constructed in such a manner that, when the stator magnetic field tries to align with the rotor magnetic field, it forms a minimum reluctance path. For that minimum reluctance path, the rotor tries to align itself with the stator magnetic field, and in that process, it gets magnetically locked with a stator magnetic field. If the stator magnetic field is rotating at synchronous speed, the rotor also rotates are synchronous speed.
In case of any overloads, the rotor comes out of magnetic locking. The rotor axis falls out of synchronism. Then immediately, there is the production of damping torque in the damper windings. The damper windings try to bring the rotor back to magnetic locking. This phenomenon is called hunting. Which is more dominant in a synchronous motor. The machine tries to hunt the synchronous state. Once the rotor is back to the magnetic locking, the damping torque or synchronizing torque disappears. The same can be concluded for underloads.
Advantages and Disadvantages
Due to its robust nature, the advantages and disadvantages of synchronous reluctance motor include the following.
The advantages are
- Due to its magnetic locking concept, the machine is able to produce constant speed under all circumstances. Any change in loads like underload or overloads will be overcome by synchronizing torque. The speed will be maintained in all respects.
- Due to the reluctance principle, it does not need any starting method like in a synchronous motor that needs starting methods and not self-starting.
- The self-starting aspect of the machine makes it more robust.
- Due to a less complicated structure, it requires less maintenance.
- There are no ripple torques like in a switched reluctance motor.
The disadvantages are
- The biggest disadvantage of the motor is that, due to its constant speed application, no speed control is possible. Since the speed cannot be varied.
- Due to the need for both stator and rotor magnetic fields, the machine is also known as a doubly excited machine. We need two excitations, one for stator and the other for the rotor.
- Due to the presence of three-phase windings, copper losses are more, as compared to DC motor.
Applications
The applications of synchronous reluctance motor include the following.
Mostly the motors are used in industry due to their property of speed control. But since the synchronous reluctance motor has a constant speed and speed control is not possible, it has very few applications. Like in conveyor belts, rice mills, paper mills, where constant speed is required.
Know more about Reluctance Motor MCQs.
Hence we have seen the principle and construction of synchronous reluctance motor. The biggest aspect of this is it is a constant speed machine. Now one must think, what are the advantages of synchronous reluctance motor over shunt motor which is also a constant speed machine.?