An induction motor is a generally used AC electric motor. In this motor, the electric current required within the rotor to generate torque is attained through electromagnetic induction from the stator winding’s rotary magnetic field. The rotor of this motor can be a wound type or squirrel cage rotor. Induction motors are also called ‘asynchronous motors’ because they operate at a less speed as compared to their synchronous speed. There are different types of induction motors available in the market and the special kind of induction motor is known as linear induction motor or LIM. So this article discusses an overview of a linear induction motor – working with applications.
What is Linear Induction Motor?
A type of induction motor that is used to attain linear motion instead of rotating motion by changing the input of electrical energy to linear motion is known as a linear induction motor. The stator and rotor in this induction motor are called primary & secondary correspondingly. The linear induction motor diagram is shown below.
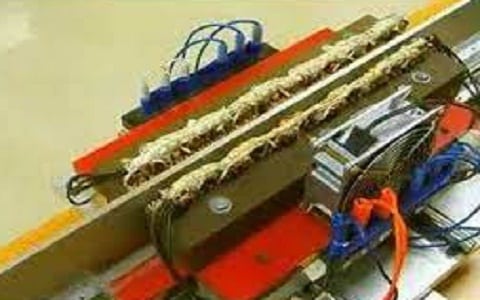
Linear Induction Motor
The secondary of this motor includes a level aluminum conductor through a ferromagnetic core. If the primary of this induction motor is connected to a 3-phase supply then a traveling flux signal can be generated through the primary length. Because of the relative motion among the aluminum conductor & traveling flux signal, current can be induced within the aluminum conductor.
So this induced current also generates a magnetic flux wave which communicates through the traveling flux signal of the primary to generate a linear force. If the motor’s secondary is permanent & the primary is free to travel, after that the force will move the primary within the traveling flux wave direction.
Working Principle
The linear induction motor working principle is related to that 3-phase induction motor however in the linear induction motor case, the stationary part like the stator is flat or unrolled as a result it generates linear forces through its length.
Linear Induction Motor Construction
The linear induction motor design is shown below which includes a rotor as well as a stator which are separated through an air gap. Generally in this motor, the stator is called the primary coil whereas the rotor is called the secondary coil (reaction plate). The stator in this motor includes a magnetic core including a 3-phase winding arranged within slots. The rotor is one kind of metal sheet designed with either aluminum or copper where current is induced.
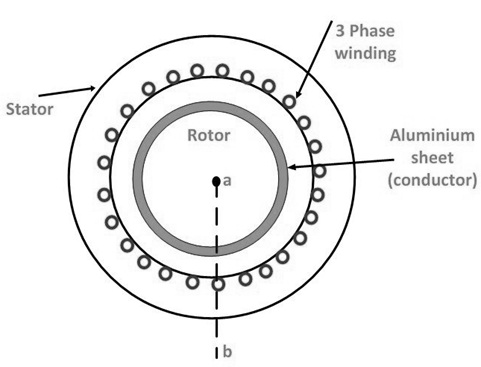
Linear Induction Motor Construction
The reaction plate width must be equivalent to the size of the assembly of the coil. The magnetic attraction among the reaction plate & and coil assembly can be balanced with a double-sided primary construction.
Working
Linear induction motor working is similar to the rotary motor but the linear induction motor has been cut & unrolled for generating linear motion rather than rotary motion. This motor includes two parts the primary & secondary.
Once power is given to the motor, these two will interact with each another but the primary must be fixed while the secondary moves.
If a three-phase supply is given to the primary of this motor then a magnetic flux can be generated which will move across the primary length. So due to this magnetic flux moving, a current will be produced within the conductor. This conductor is designed with aluminum material within the secondary linear induction motor.
The current induced within the secondary of this motor will interact with the traveling flux & generates a linear force or linear motion. If the secondary in the motor is fixed & the primary moves, then force will move the primary toward the traveling wave.
As we discussed, the 3- phase supply is provided to the stator winding, then a magnetic field can be formed. So this field moves at a liner synchronous speed which can be given as
Vs = 2τf m/ sec
Where
‘τ’ is the Pole pitch in the meter.
‘f’ is Frequency in Hz.
Here the synchronous speed is not directed through the number of poles and any preferred linear speed can be attained by changing pole pitch. When flux moves linearly then it induces currents within the rotor plate. So, the induced currents interacting through the field generate thrust on the rotor plate & pull the rotor plate in a similar direction.
Similar to a cylindrical induction motor, this induction motor also works at below synchronous speed because it can’t run at synchronous speed. When this motor is an induction or asynchronous motor, therefore the secondary coil speed is not high at the synchronous speed. The main difference between these two speeds is called slip. So the linear induction motor’s slip can be given by,
Linear induction motor slip (s) = (vs – v)/vs
Here, the linear force or thrust can be controlled by simply changing both voltage & frequency so that the density of induction will stay constant.
Characteristics
The characteristics of a linear induction motor include the following.
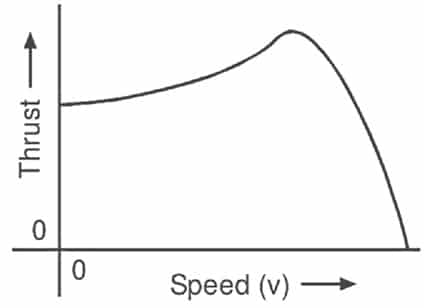
Speed vs Thrust Characteristics of Linear Induction Motor
In a linear induction motor, a force-generating the linear motion is known as thrust. Here the thrust force characteristics of the LIM are shown below. These characteristics are the same as the torque-speed characteristics of conventional induction motors.
Whenever this motor begins from an inactive condition & speeds up to a synchronous speed, then thrust force attains a maximum at a translation speed & after that, it falls. This is due to the amount of difference within the magnetic flux in the aluminum sheet being decreased when the difference in the magnetic field produced through the coil attains a synchronous speed. Let us see
Why use an LIM?
LIMs are suitable for applications that require high-precision, low-power movement over long distances and high speeds. They’re ideal for automation and robotics applications, as well as in requirements which need to move something with precision but not too much force—for example, moving objects from one place to another or positioning them precisely in relation to other objects (such as when working with semiconductor manufacturing equipment).
What is the difference between a linear induction motor and a regular induction motor?
Linear induction motors have a magnetic core that is fixed to the stator, which helps to maintain alignment with the rotor. This means that there is no need for an external power source or control system to keep the rotor properly aligned with the stator. In addition, because there is no need for brushes or slip rings, linear induction motors are much simpler than standard induction motors.
Does the induction motor require any maintenance?
No, the induction motor does not require any maintenance.
Advantages
The advantages of a linear induction motor include the following.
- These motors are not expensive.
- Simple construction.
- Maintenance cost is less because of the deficiency of rotating parts.
- There is no limitation for maximum speed because of centrifugal forces.
- These are used in long-length applications because they don’t have secondary parts.
The disadvantages of linear induction motors include the following.
- This motor has a larger air gap which is typically 25 mm, so it results in less power factor.
- This motor has higher rotor resistance.
- The larger air-gap & non-magnetic reaction rail requires more magnetizing current which results in a low-power factor & poor efficiency.
- As evaluated with a conventional rotary induction motor, this motor needs a larger air gap.
- This motor draws a large magnetizing current than a rotary induction motor with a similar rating.
- The power factor & efficiency is low as compared to a conventional induction motor with the same rating.
- The enhanced physical size of the device needs a larger package size.
- The efficiency of this motor is low & they generate more heat.
Applications
The applications of linear induction motors include the following.
- These are appropriate for heavy-duty applications.
- These motors are most extensively used in high-pressure applications, wherever stable force ratings of almost 25gms of acceleration & hundreds of pounds are necessary.
- The main application of this kind of induction motor is in transportation wherever the primary is arranged on the vehicle & the secondary is laid through the track.
- These help handle materials in cranes.
- These are mainly used for liquid metal pumping.
- Used like an actuator for movement of the door.
- These are used within high-voltage-based circuit breakers.
- These motors are utilized within accelerators for rigs to test the performance of the vehicles in impact conditions.
- These are used in conveyors, electromagnetic pumps & trolley cars.
- This motor has power over a cylindrical induction motor for >200 km/h speeds. So it provides an outstanding motive power source for magnetically balanced trains wherever the cylindrical induction motor stops working.
know more about:
Three Phase Induction Motor MCQs.
Thus, this is all about an overview of a linear induction motor. This is an asynchronous motor that works on the principle of an Induction Motor; however, it is mainly designed to generate the rectilinear motion. This motor is an advanced version of a rotating induction motor that provides a linear translational motion in place of the rotational motion. Here is a question for you, what is the performance of the linear induction motor?